The Season of FEST23
A Brief Overview of the Season
5 competitions, 50 days, and over 50 students putting 10 months of development to the test – this describes what awaited the team before heading to Europe for competition. On the evening of July 10th, we started the buses to embark on the first competition of the season. 2400 kilometers and a day later, we arrived at the Dallara car factory parking lot around 4 o’clock in the morning to give the FEST23 the final touches and prepare it for technical inspections. At 8:30, we entered the competition area, and the first race of the season began!
On-site, we faced sweltering heat, as if there was a wall of heat when we stepped out of the team bus. Suddenly, temperatures were nearly 20 degrees higher than what we were used to in Estonia. This was the first challenge for both the team and the formula car. The extensive preparation paid off, as we were one of the first teams to pass technical inspections and were allowed onto the track. The good reliability of the formula car that started in Estonia continued in the central European heat, and the first events went smoothly. The track conditions were excellent, and the team had never seen such high longitudinal and lateral acceleration values. We were very satisfied with the performance and the first test, and our biggest competitor in the competition was a German team holding sixth place in the world rankings. We were leading in the overall standings until the driver change, when Robert-Juss took the wheel. We had to slow down significantly because the temperatures inside the monocoque rose so high in the sun that the inverter’s maximum temperature was within reach. The Germans had a special refrigerator with them to cool the battery pack before going on the track. It was not prohibited in our pit box, so hats off to them for a well-done solution. We finished second overall! A very good result for a completely new concept formula car in its first competition. The electronics were reliable, and there weren’t too many sleepless nights where something major needed to be done. After the competition, we earned a day off on the shores of the Mediterranean in Venice, which was halfway to Austria, on the way to Graz.
The local team agreed to host us before the FS Austria competition. We got almost a week of valuable testing and fine-tuning time. The last testing day in the mountains was rainy, with the rain having just stopped, and it seemed like a good time to charge the battery pack. As soon as we removed the battery pack from the formula car, it started pouring. We tried to protect the battery pack as much as possible with umbrellas and a tent, but moisture still got through, and the measured insulation indicated a problem. The electronics team searched for the issue for a whole day, but found nothing. Time was running out, other teams had already passed technical inspections at the competition venue, while we were diagnosing the battery pack two hours away. Long story short, the relief was immense when the faulty multimeter turned out to be the issue. We packed our things and rushed to the Red Bull Ring in Spielberg. Straight to technical inspection, and the next problem – according to the chief judge, our module housing material did not meet the required fire resistance standards. Despite a lengthy debate, reference to the rules, and explanations, the judge remained firm and did not allow us to pass inspection. We considered various options, but making a new module housing in such a short time was not possible. We had to find a solution with existing materials and quickly. We found that if we took two 3mm thick pieces of housing instead of a 2mm thick one and soaked them with water in between, the material would be sufficiently fire-resistant and self-extinguish. Somewhat skeptical, we went to the judges, and behold, they took a look and it was approved. Quite strange.
The rest of the inspections went smoothly. Since we had extra time, we could test the last parameters in the test area. Both static and dynamic events went well, and a podium finish was in sight in the overall standings. The last and decisive event – endurance race. FS Team Tallinn is on the starting line, the team is ready at the computers, monitoring telemetry, the formula car takes to the track, the driver drives cleanly, and the car is fast. Until the moment when it’s not. The safety car’s warning light reveals that the high voltage has been disconnected, and the formula car is just rolling. The endurance race was over for us. At the end of the long straight at the Austrian track, there is a sharp turn, which means a high-speed deceleration from top speed, which entails a significant deceleration with regenerative braking, where the battery is charged. There is a limit to how much the battery can handle. The code regulating regenerative braking with electric motors had been used by the team for the past three years without any issues. It’s just unfortunate that the problem surfaced at the most critical moment, but that’s motorsport. Heads up and onwards. The car is one of the fastest in the world, and there was still time to prove it in the next three competitions.
Before the awards ceremony, there was a small window of free time, so we collectively decided to hike to the nearest mountain peak to clear our heads. With the group you’ve been working hard with for the past 10 months, you can tackle anything. The mountaintop was conquered. The Estonian flag was raised, and Team Tallinn was cheered on. There were actually several achievements to take with us.
We headed to Hungary for the next competition, but this time we couldn’t take a beach break, as we needed to attach the autonomous system. Hungary was the first competition of the season where we drove both with a driver and autonomously. The Hungarian competition went fairly smoothly; we were satisfied with both static and dynamic events. In the design presentation, the team had never achieved first place in a competition with such high competition. Definitely one of the proudest achievements of the season. Although it was the first technical inspection with the autonomous formula car, we passed it before any driving events. The brake test required a few attempts because initially, the system tried to navigate through the cones in a slalom. Some modifications, a smooth acceleration to 40 km/h, and a sudden stop, well done. Now we could take the autonomous car to the track. In Hungary, we had to contend with stormy weather at times, which disrupted both overnight camping and dynamic events. For example, we were removed from the starting order for the autonomous car cross race because a storm was imminent. We waited in the pit until it drizzled for a while, and then the area was reopened, 25 minutes before the final closure. We got the car to the starting line, but the formula car couldn’t execute the correct commands. The calculated trajectory on the log seemed correct, but the formula car turned towards the cones. The endurance race with a driver took place in the rain, which suited us very well – it was like home conditions for FEST23. We set some of the best times of the day together with the Stuttgart University team, and there was intense competition at the front. On the 16th lap, our formula car disappeared around a corner and didn’t come back – did the driver go off track? Did something happen to the formula car? Uncertainty. After a long radio silence, we heard from the driver – it’s over. There was a poor connection at the measurement point in the battery pack, and to avoid major problems, the battery management system issued an error message. Again, no problems in the previous 500 kilometers, the error occurred just during the endurance race.
We headed back to Győr to prepare for the next race. The failed endurance races were bothering us, and we definitely wanted to complete one more endurance race before the next competition. Since the local team didn’t have very good testing opportunities, we drove 5 hours to Slovakia to another friendly team who had the track reserved for the next day. The long journey was worth it; we completed an endurance race without any issues, which gave us confidence for the upcoming race in Germany.
The German competition is the largest in Europe, with over a hundred teams participating. This season, it was our fourth race. Overall, everything went successfully; in the eighth race, we managed to achieve the day’s best lap time, and elsewhere, we were constantly competing for the podium. By the time of the German race, most teams had improved their cars and offered tough competition. We managed to break the bad luck that had followed us in two races, and despite a very uneven track that caused suspension problems for many formula cars, we completed the endurance race! The emotion was overwhelming, and almost the entire team had tears of joy in their eyes! We had never before completed an endurance race in Germany! This achievement will be remembered by everyone, and in such a high-level competition, we can consider ourselves in the top six.
Right after the awards ceremony in Germany, we headed to Croatia for the last race of the season. The FS Alpe Adria competition was new for our team. Despite having four races behind us, most technical issues were discovered there during the technical inspections. The judges meticulously inspected every small detail. We were really in our element at this competition. In the static events, we were in the finals for both design and cost report, which is quite a rare occurrence. In the dynamic events, we achieved second place in acceleration and autocross, and for the first time this year, we secured third place in the qualification. We hadn’t gathered so many podium finishes in a single competition this season.
In the grand scheme of things, we can conclude on a positive note. The new concept works, the team was well-prepared for the races, strong in the dynamic events, and one of the best in the static events. This is the result of years of systematic work, dedication, and knowledge transfer. Five design finals in the last nine races, three wins in the design category, two podiums in the cost report, all in a single season. Such statistics cannot be boasted by Zurich, Munich, or any other top engineering university in Europe. We are the ones up there, from this small Estonia. Proud!
Last season, luck was on our side, and despite constant reliability issues with the car, we managed to get FEST22 running miraculously for the competition. This season was quite the opposite. We worked diligently to improve reliability, and all the errors from the previous year were fixed. FEST23 had over 500 test kilometers behind it, during which the car performed flawlessly and demonstrated good reliability. During tests, we always managed to complete the endurance race, but problems arose during the competitions that had never occurred before.
This season confirmed that the student formula is truly a journey to the top, and despite some setbacks, FS Team Tallinn’s level is such that the world’s best must watch our progress with concern. The work done here also stands out to others, and team members managed to receive job offers from Rimac, Volkswagen, Tesla, and BMW Motorsport – the whole world is open to us!
We then went to Hungary, where the FEST22 and driverless car teams met again. Unlike Austria, everything went smoothly there. Technical inspections went smoothly and we achieved good results in static events – both cars earned decent points in the cost report, and we managed to get to the design finals with FEST22. Adding podium places in driving events, second place with FEST22 and third place with the autonomous car were guaranteed in the overall standings!
After a pleasant success, we went to Germany for the season’s final and most prestigious race. Although the same data logger was used there as in Austria, with the judges’ guidance, we got it working. The static events went perfectly, we achieved 3rd place in the cost report, and reached the design finals. Reaching the design finals in Germany and winning third place at autocross, are definitely some of the biggest achievements of the team!
FEST23 Stats
2.7 s
Acceleration
185 kg
Weight
1250 Nm
Torque
2.8 G
Max. lateral acceleration
760 N
Downforce (55 km/h)
140 kW
Combined power
Gallery
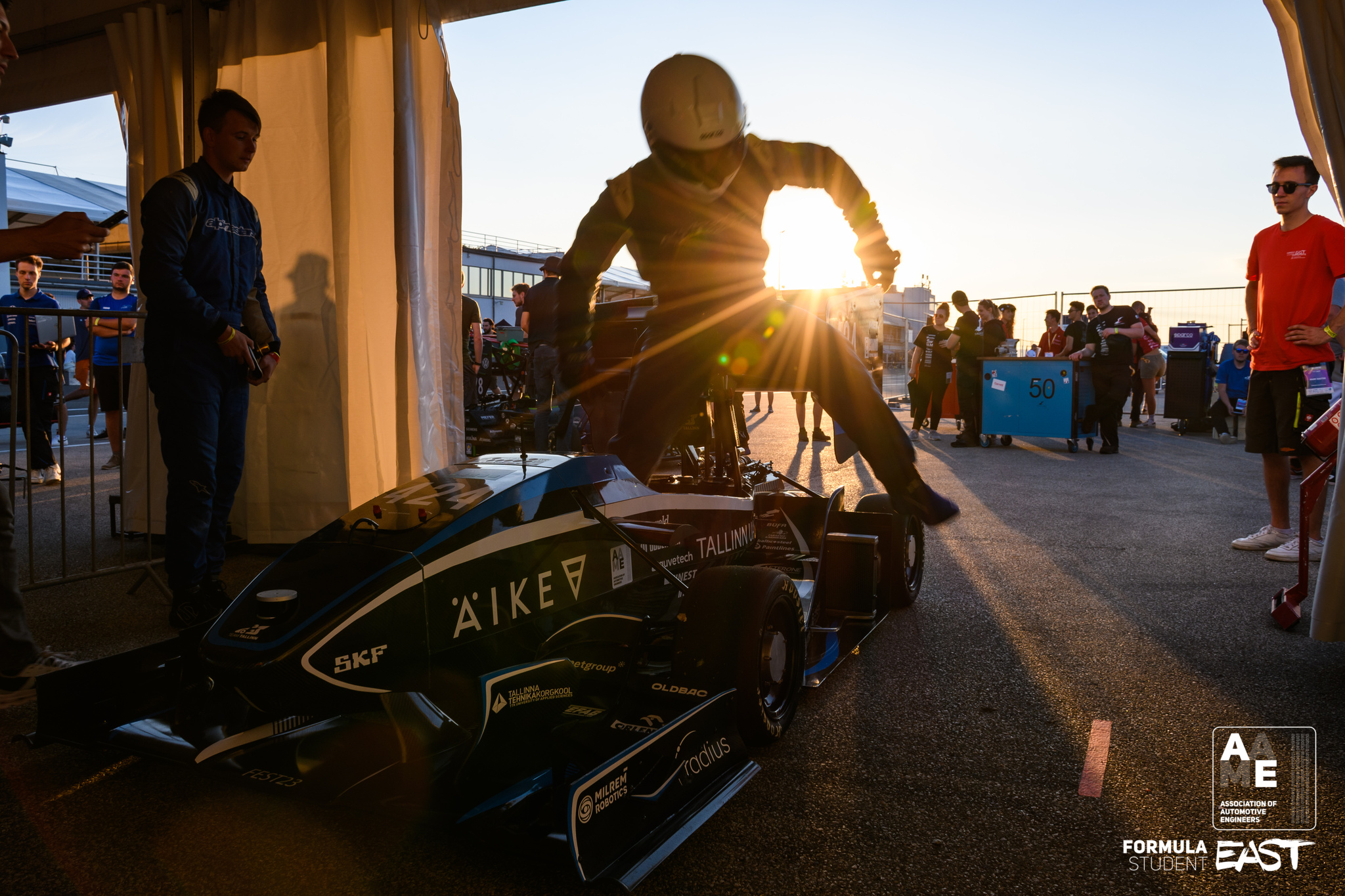
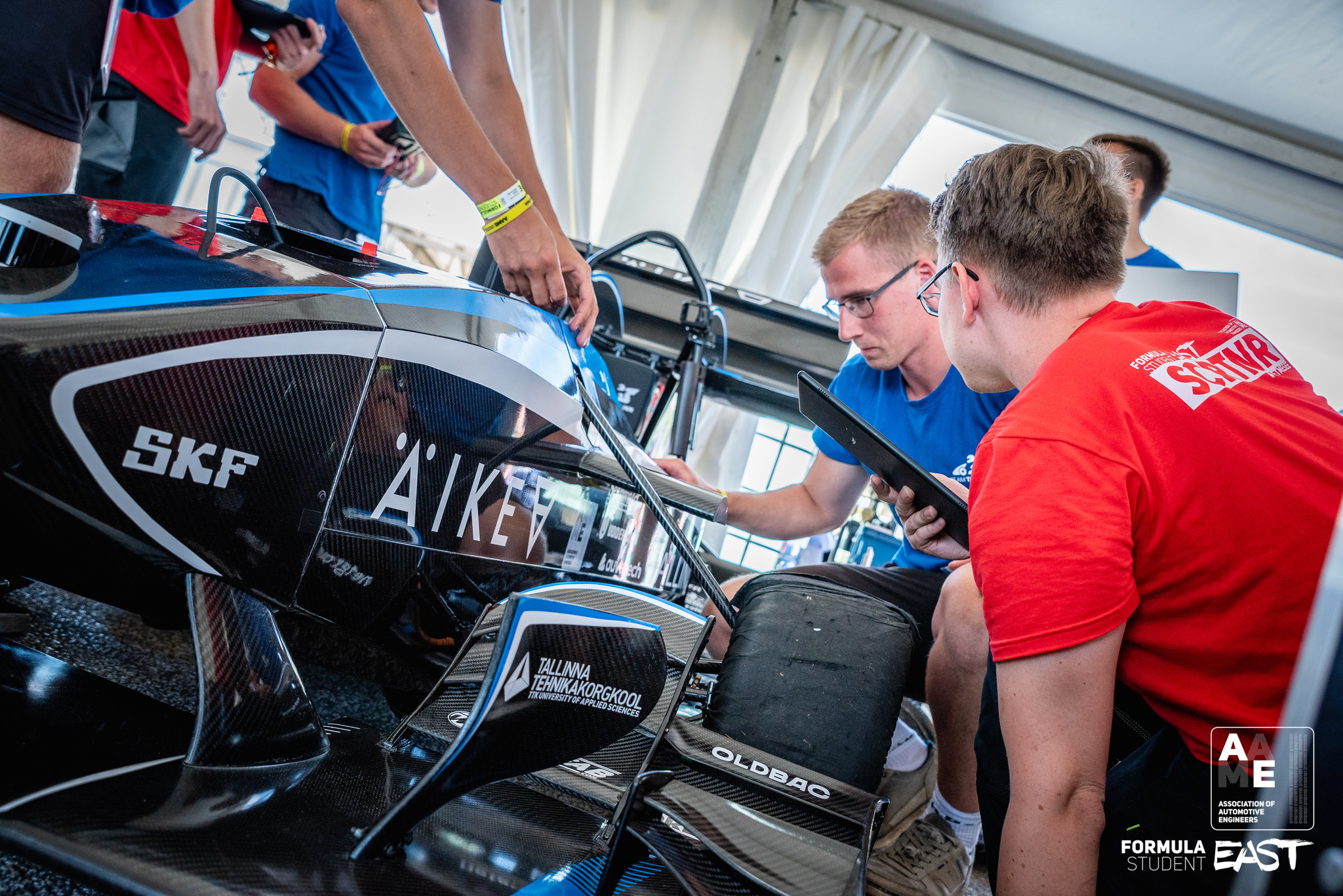
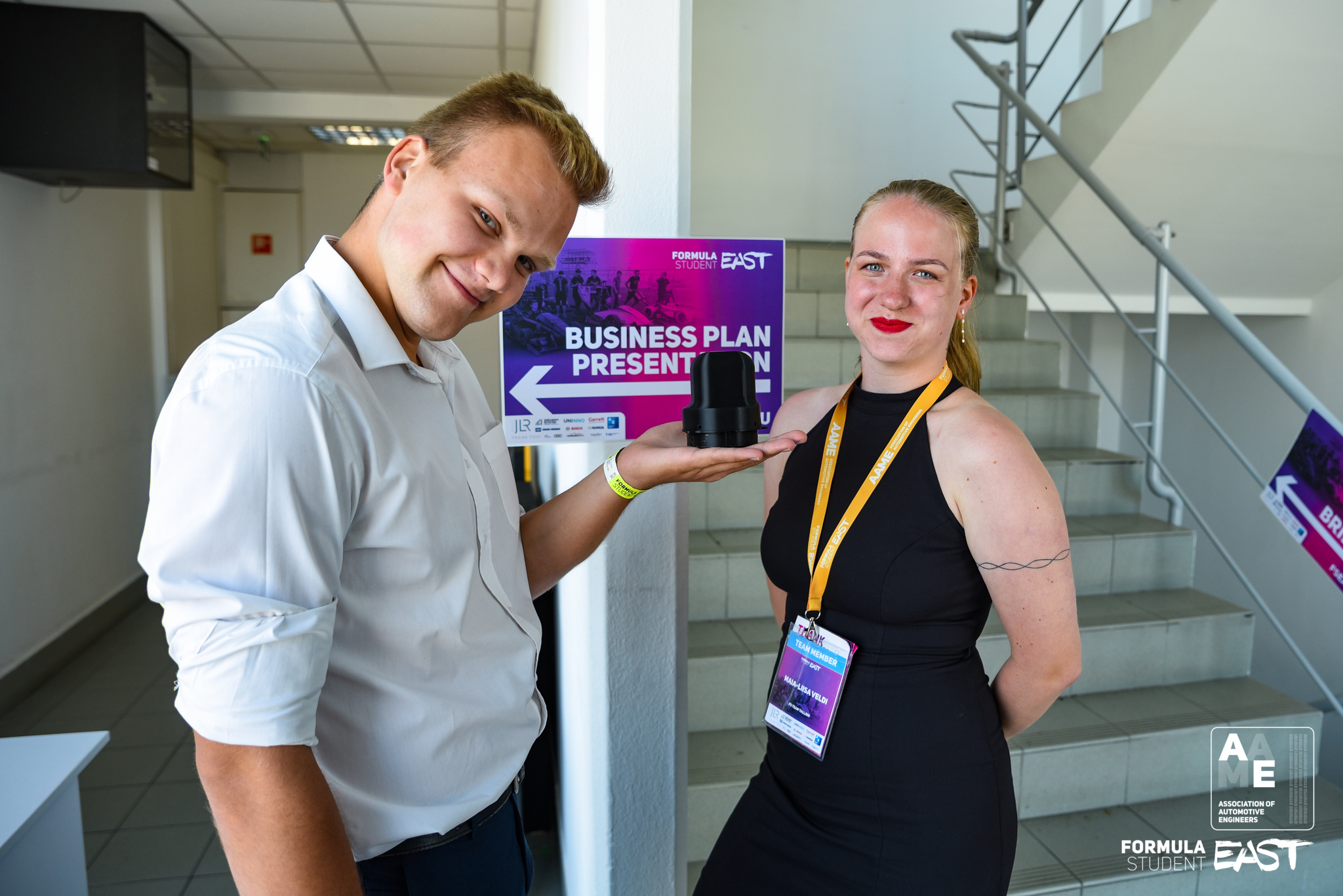
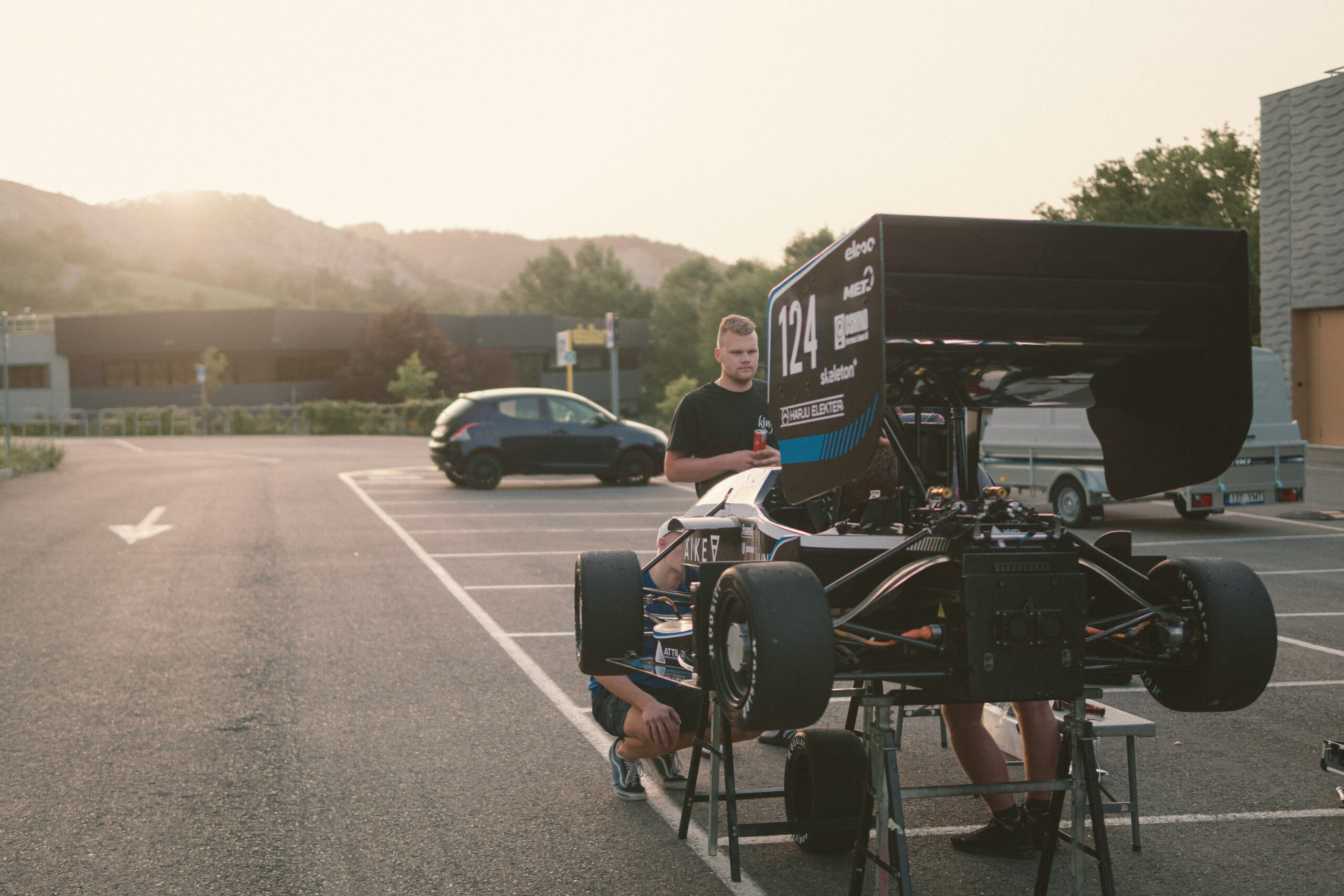
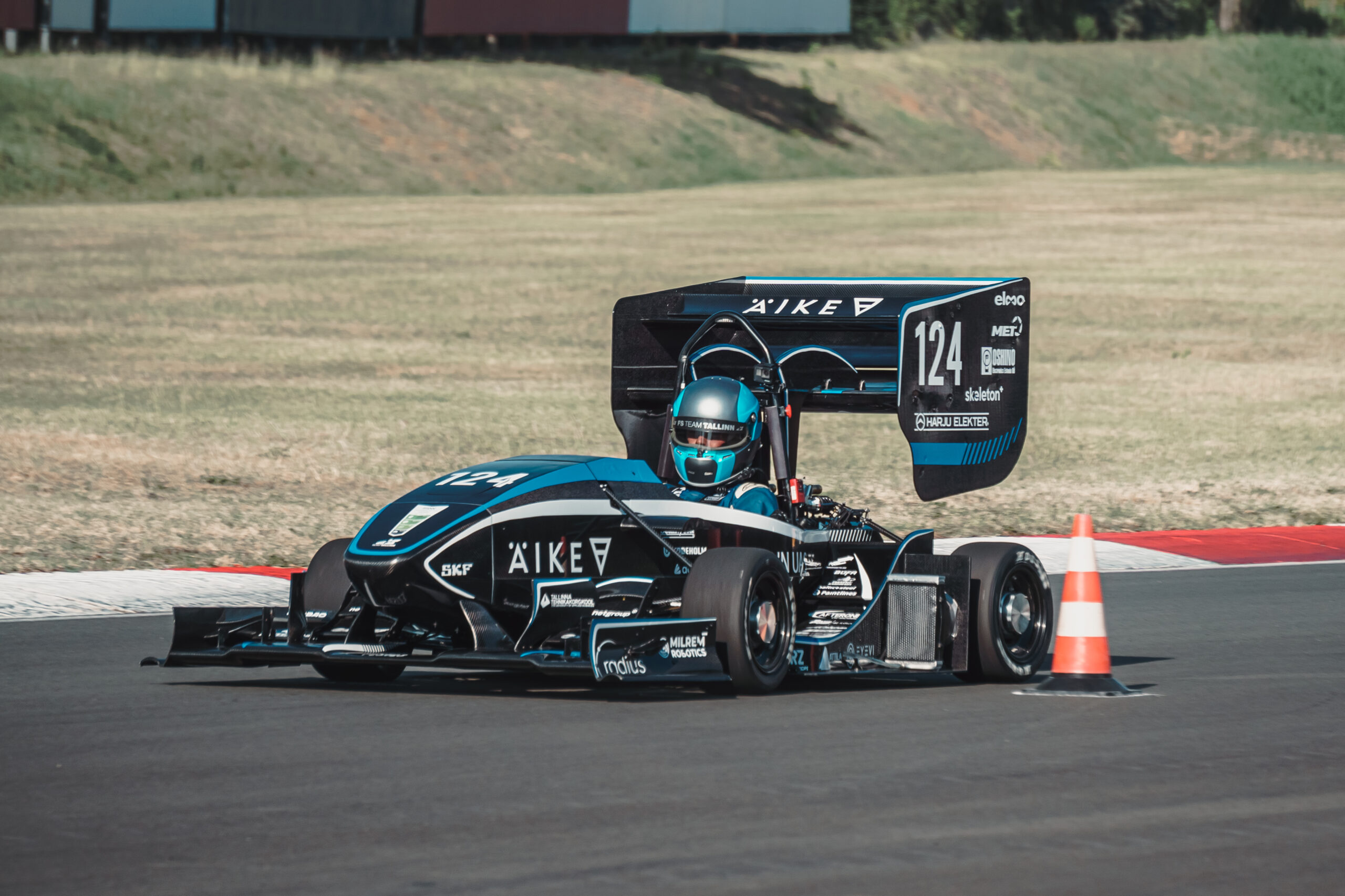
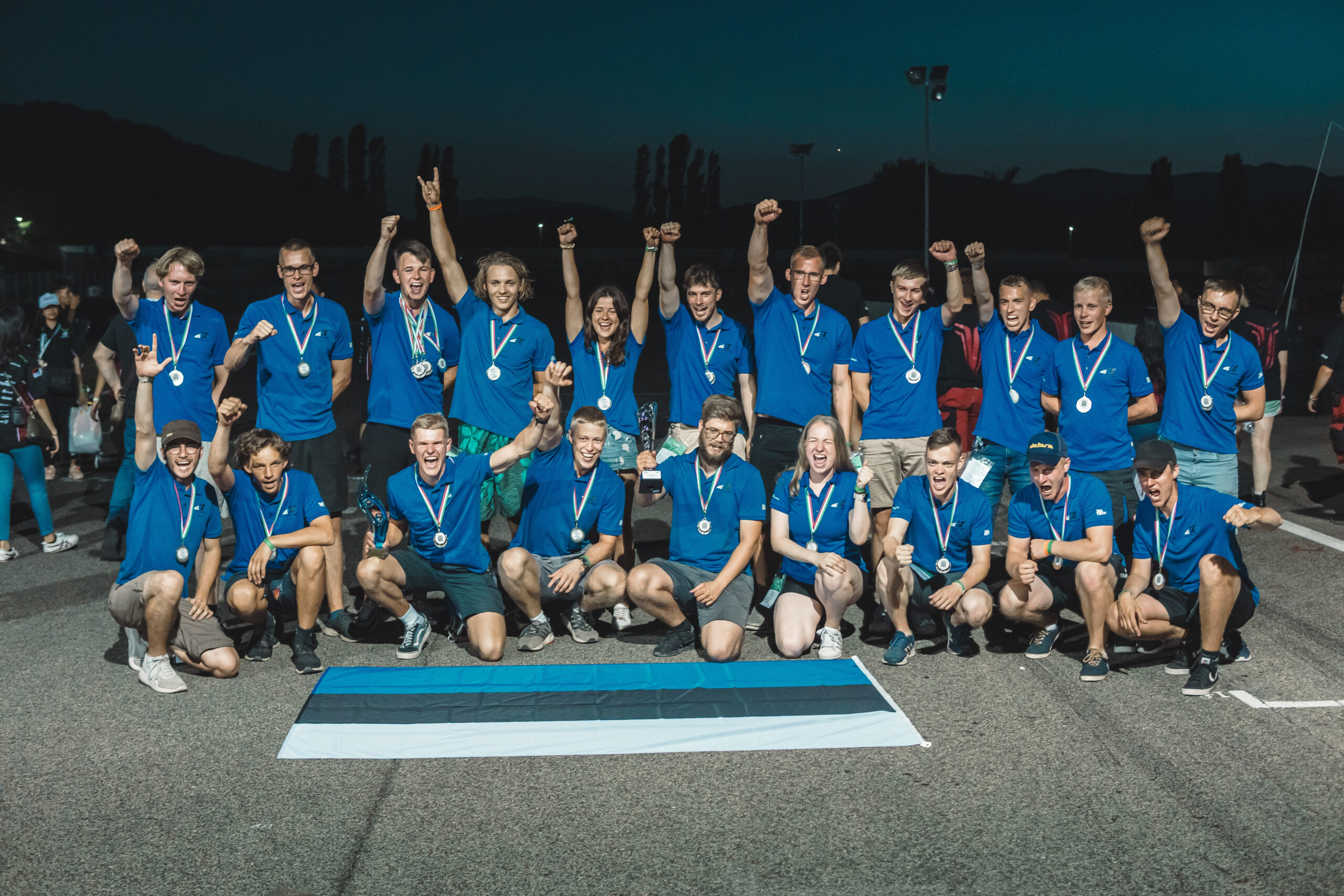
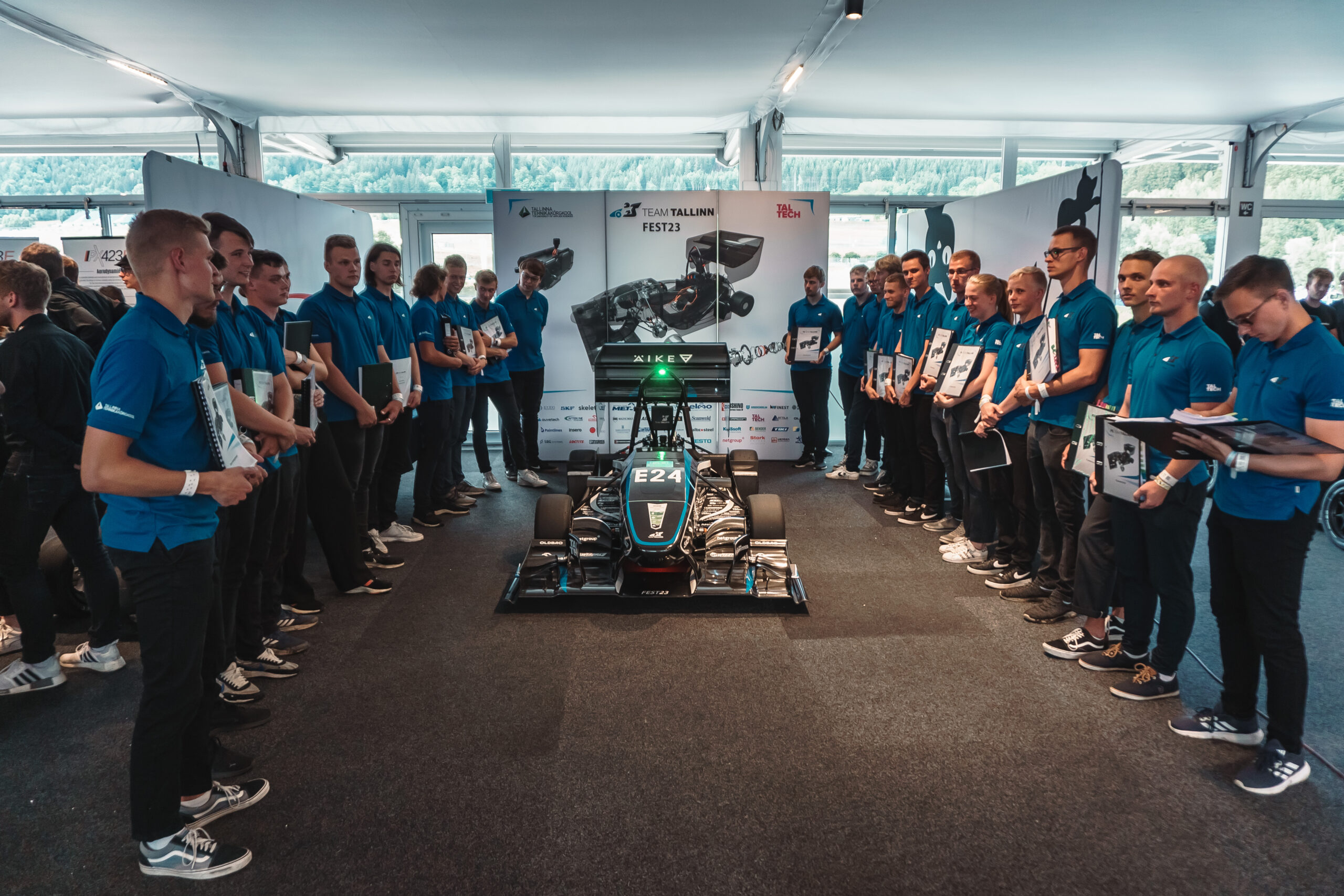
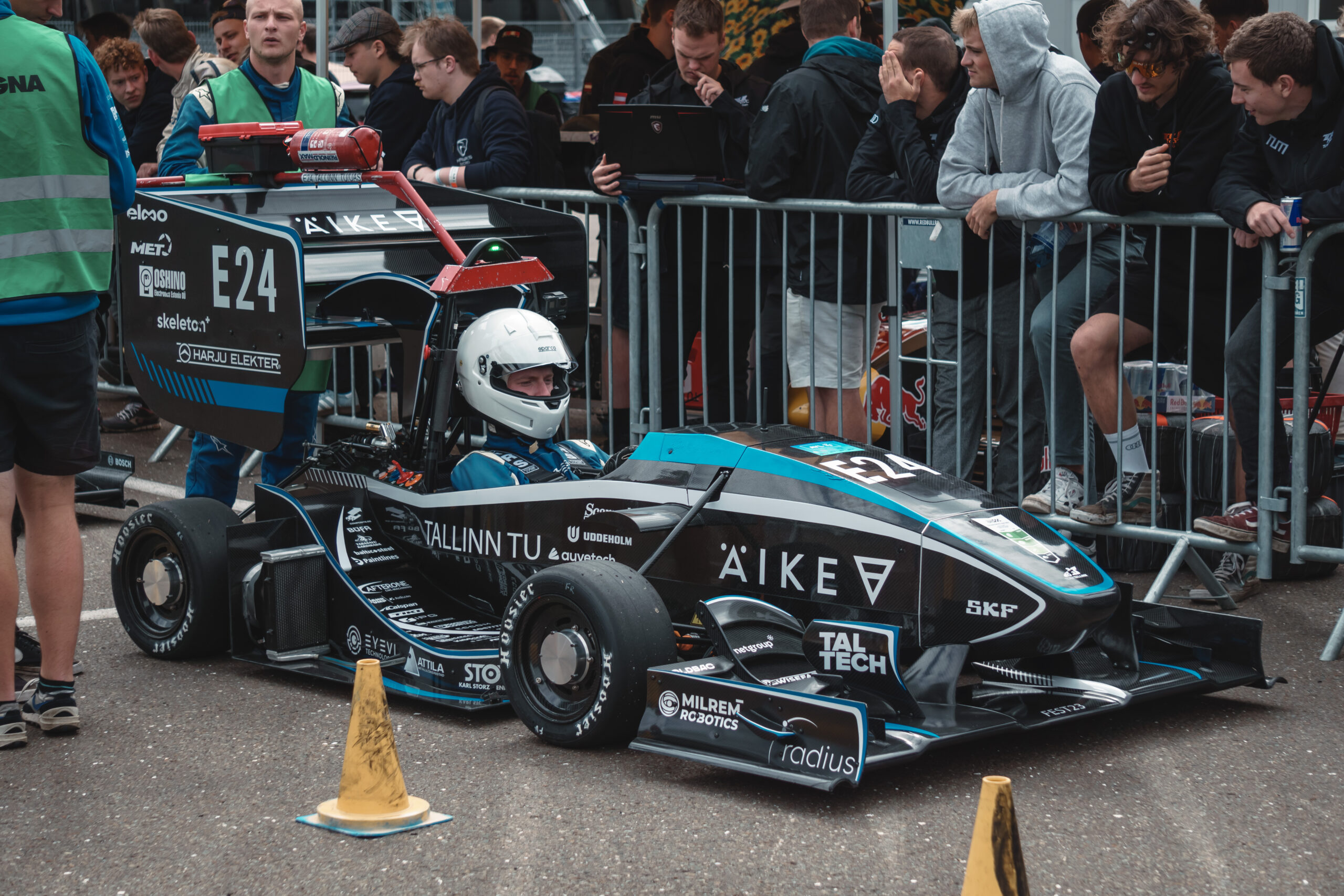
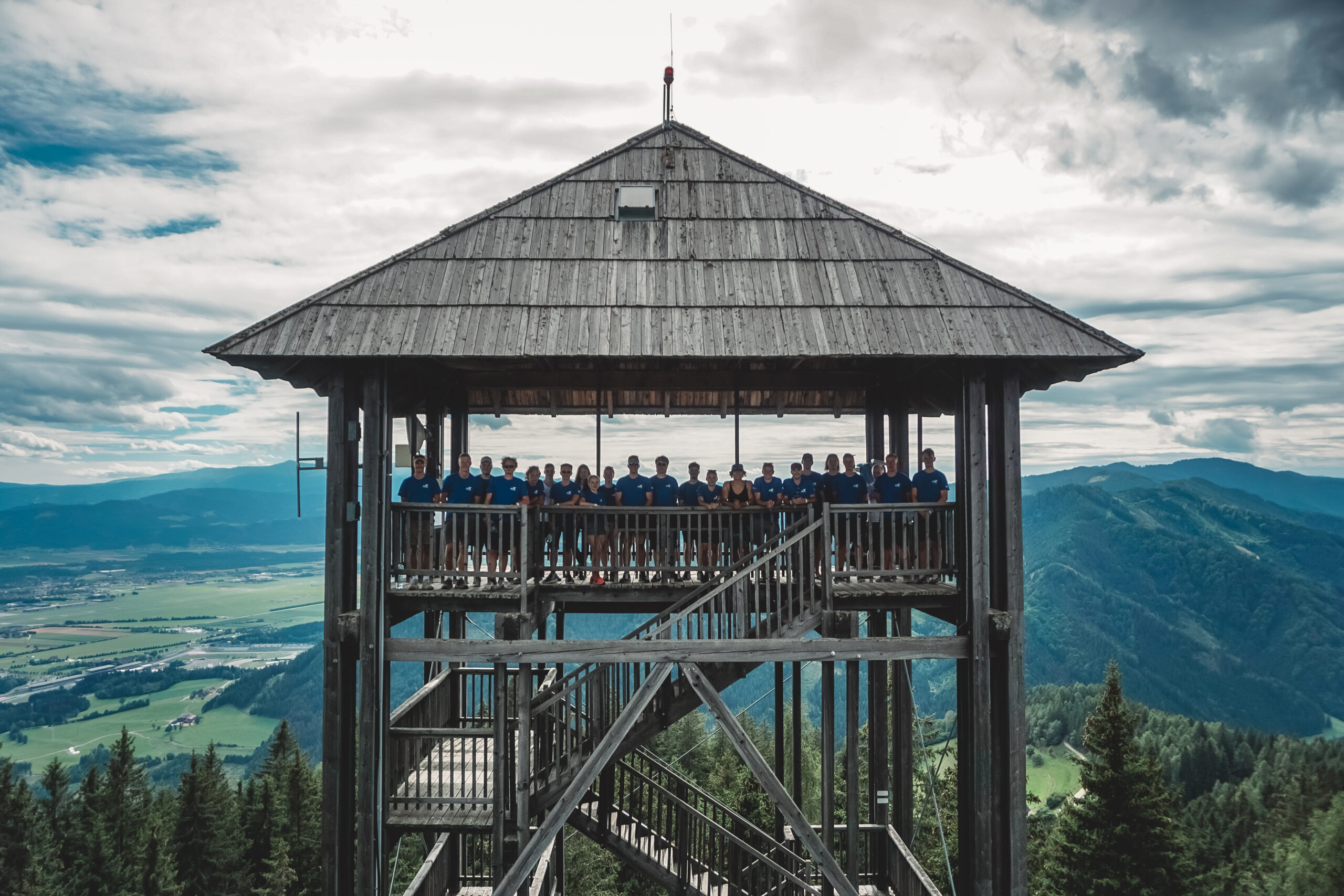
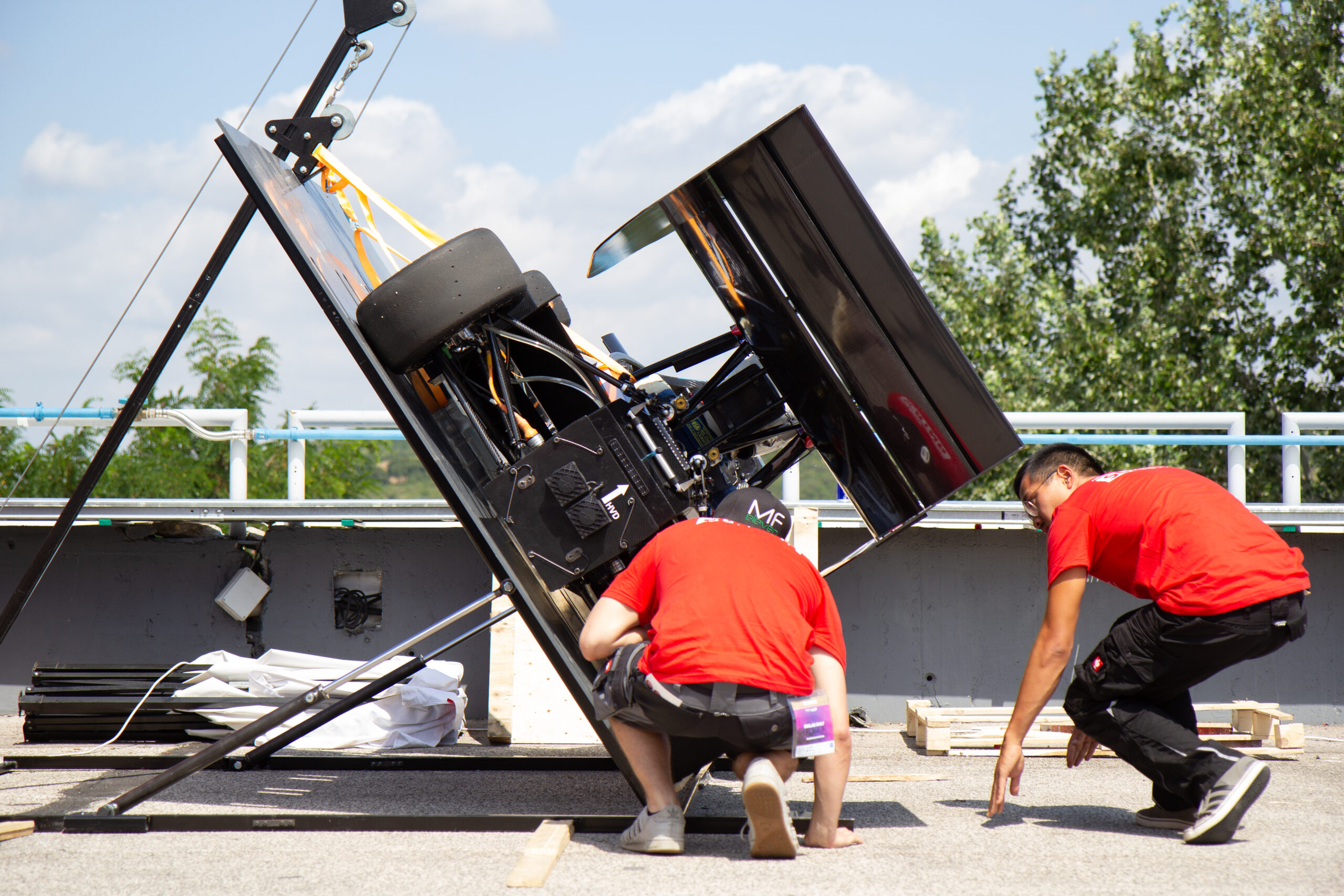
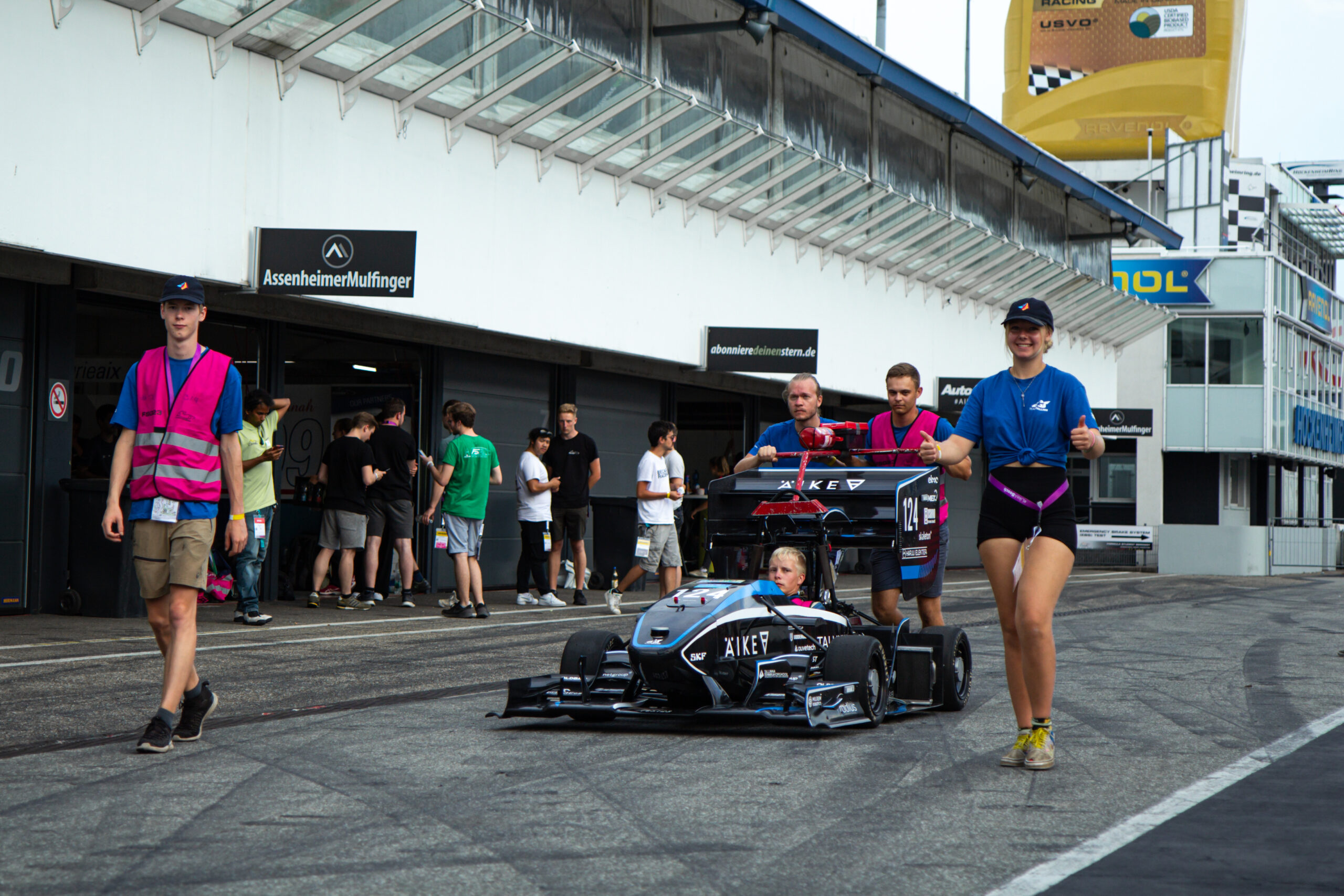
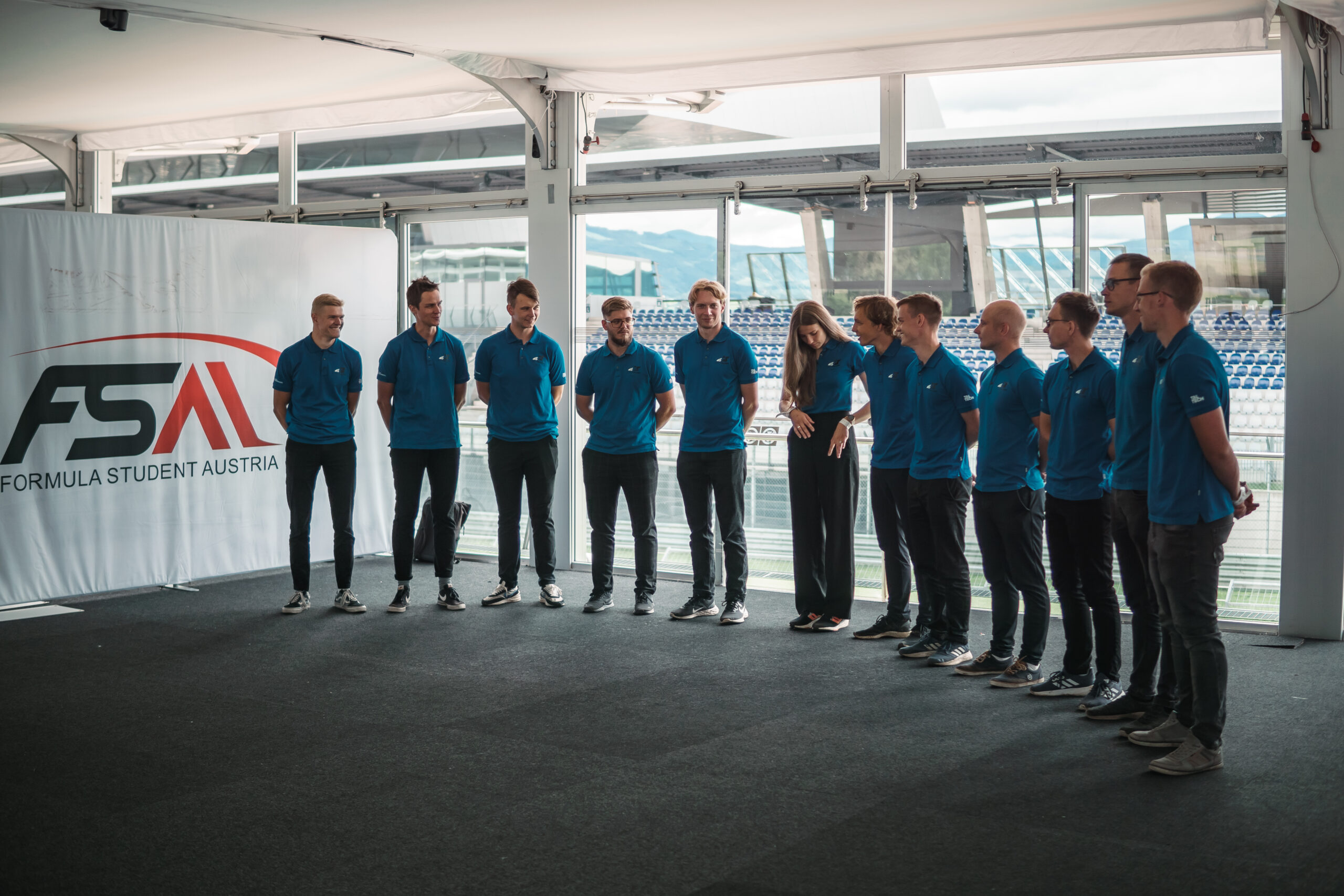
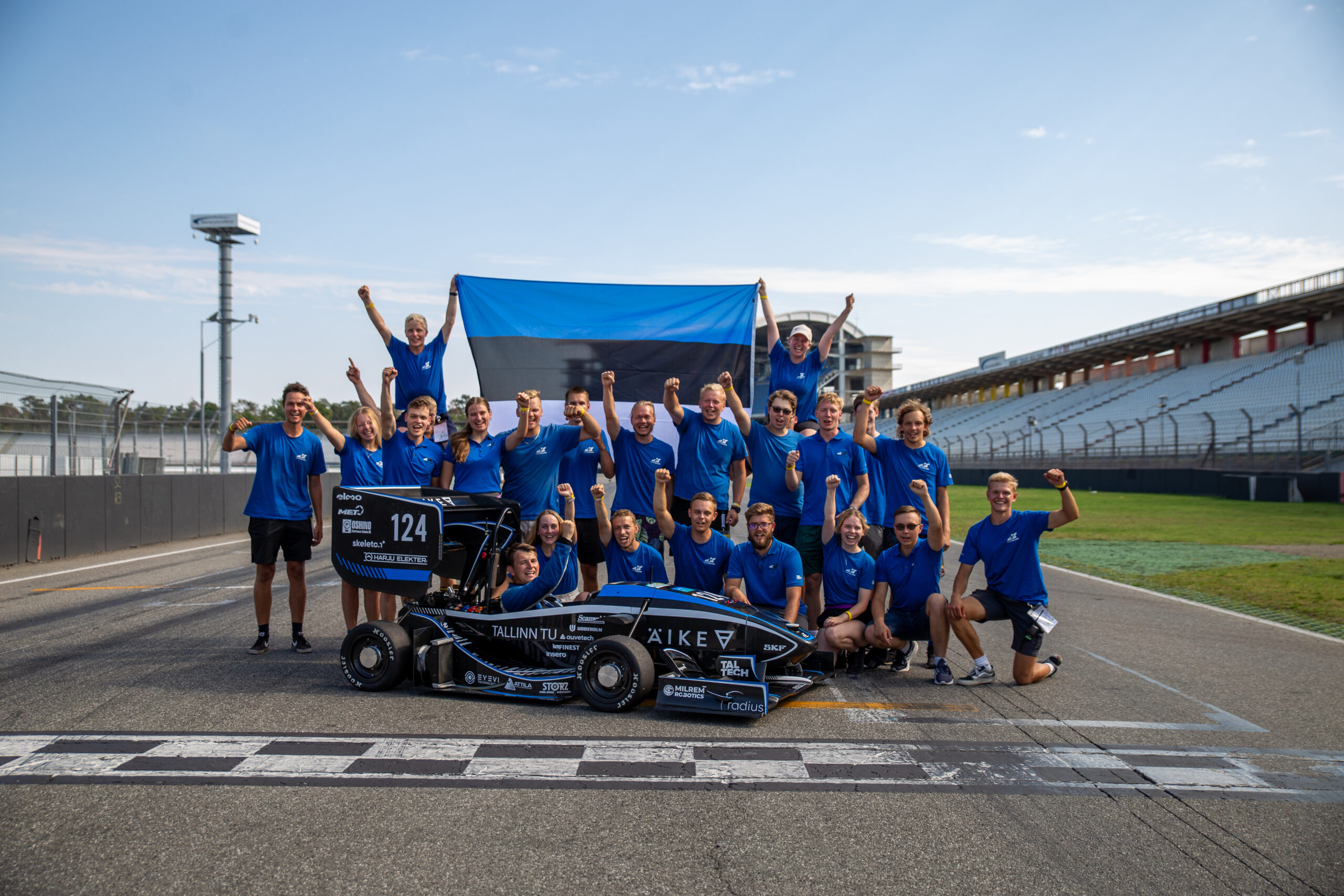
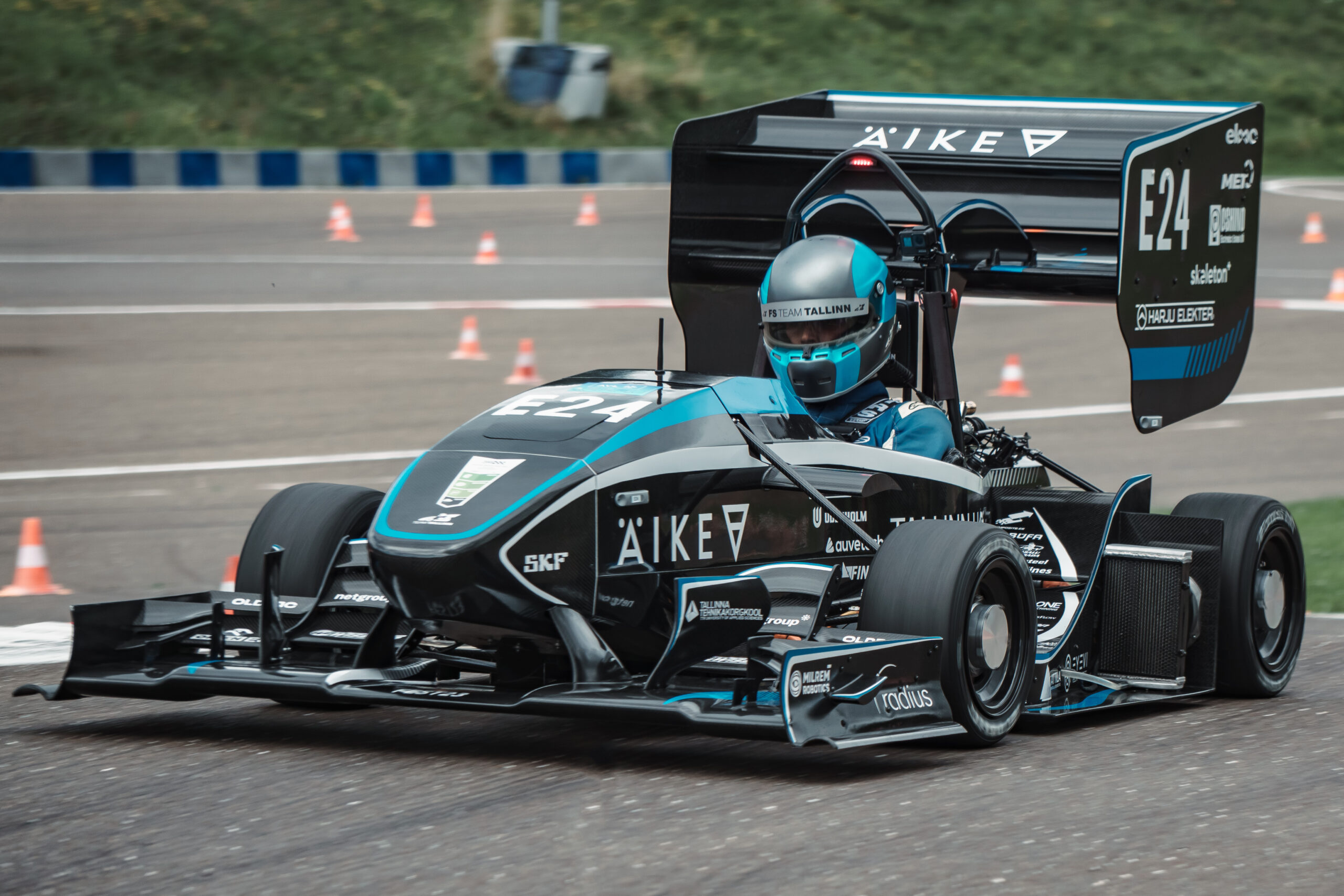
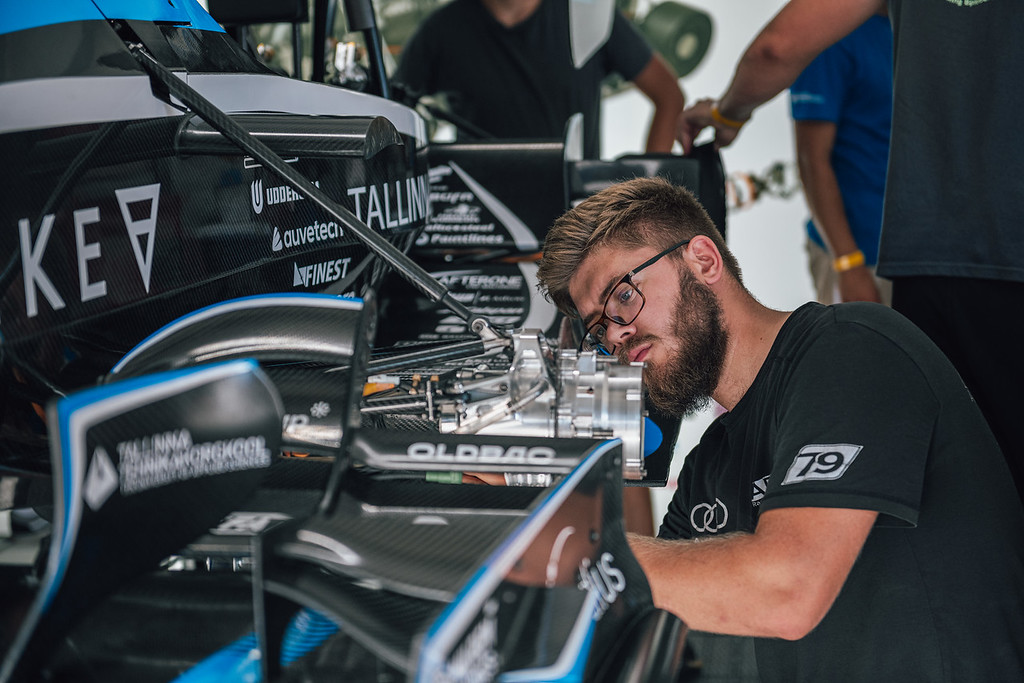
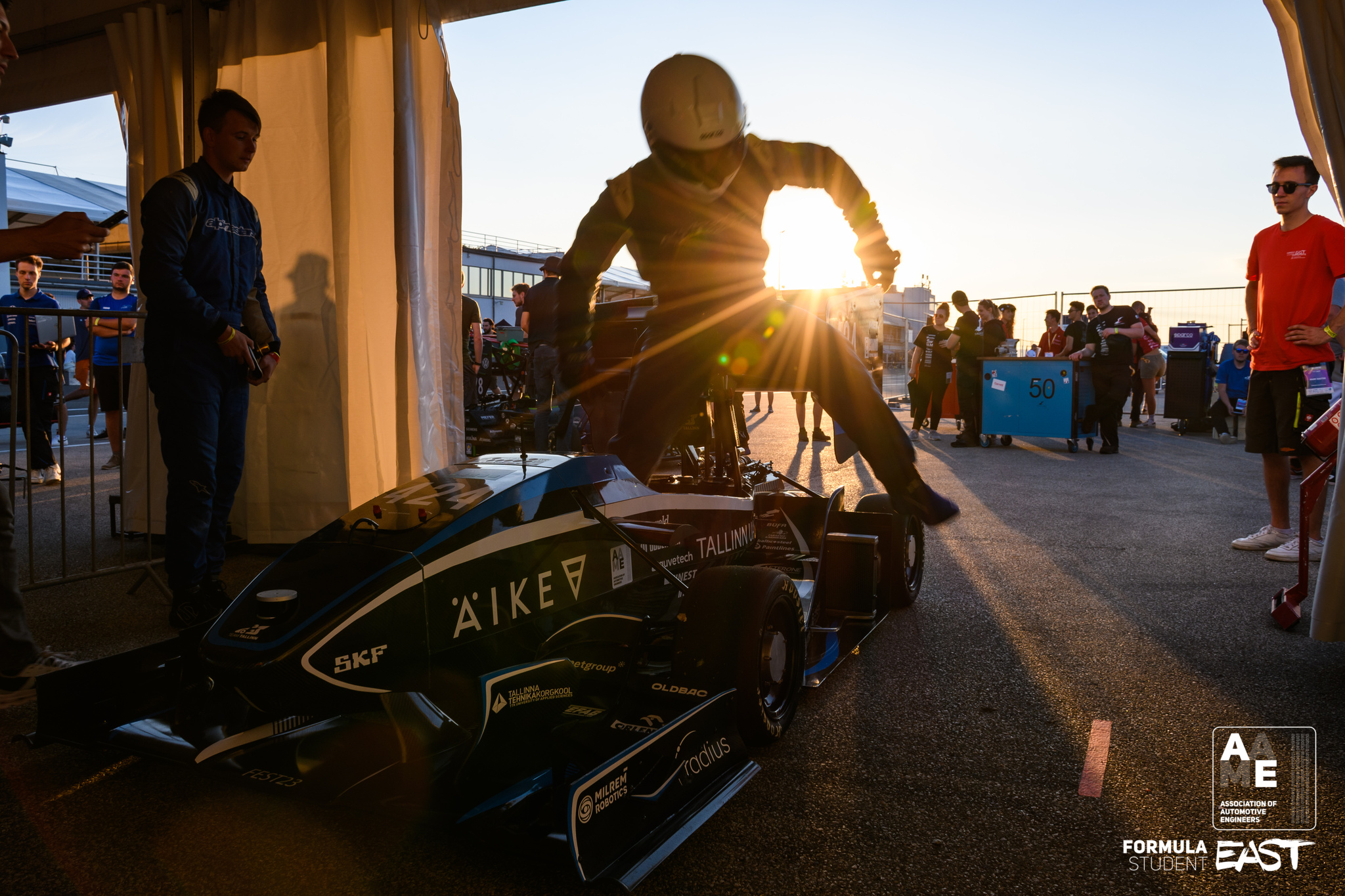
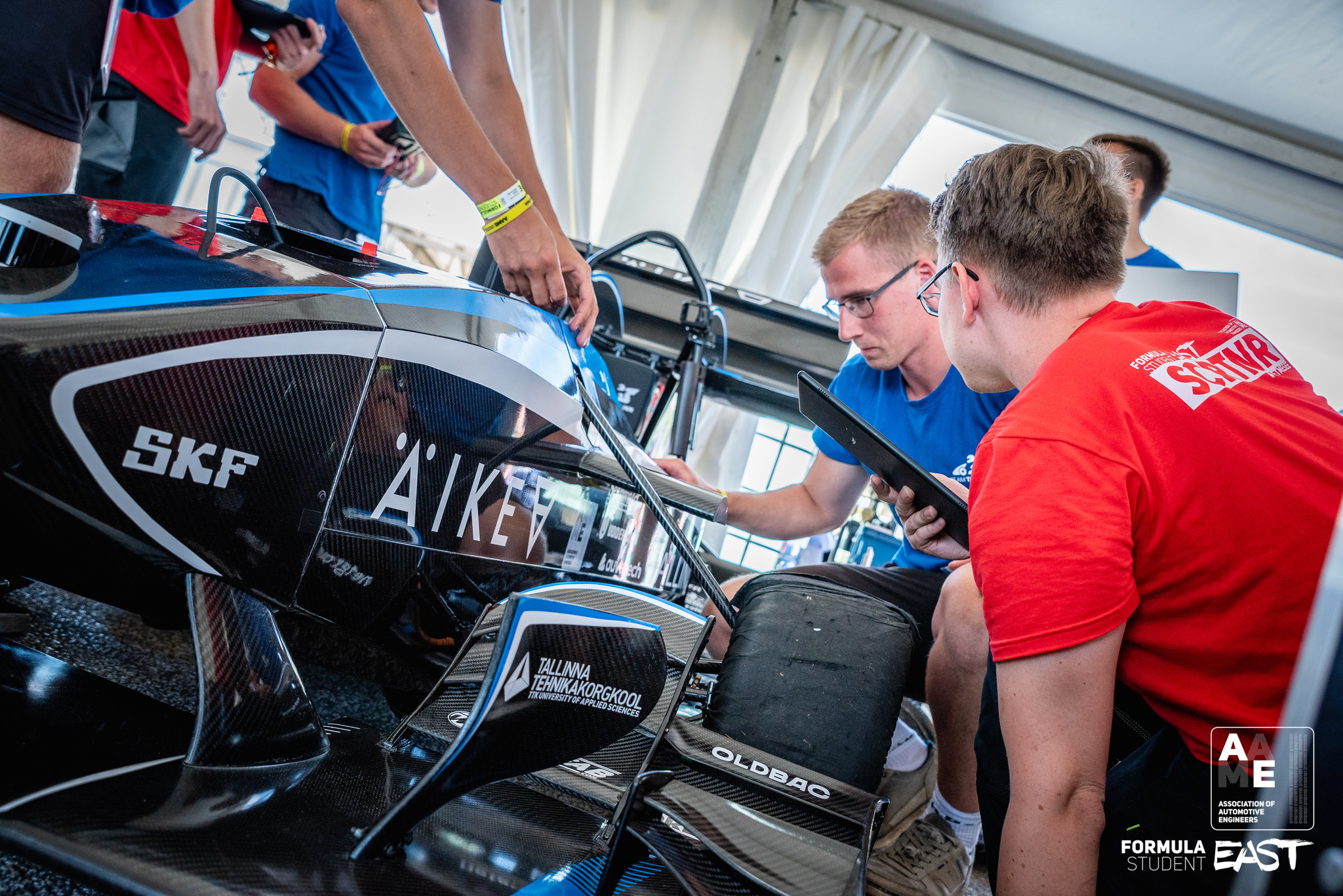
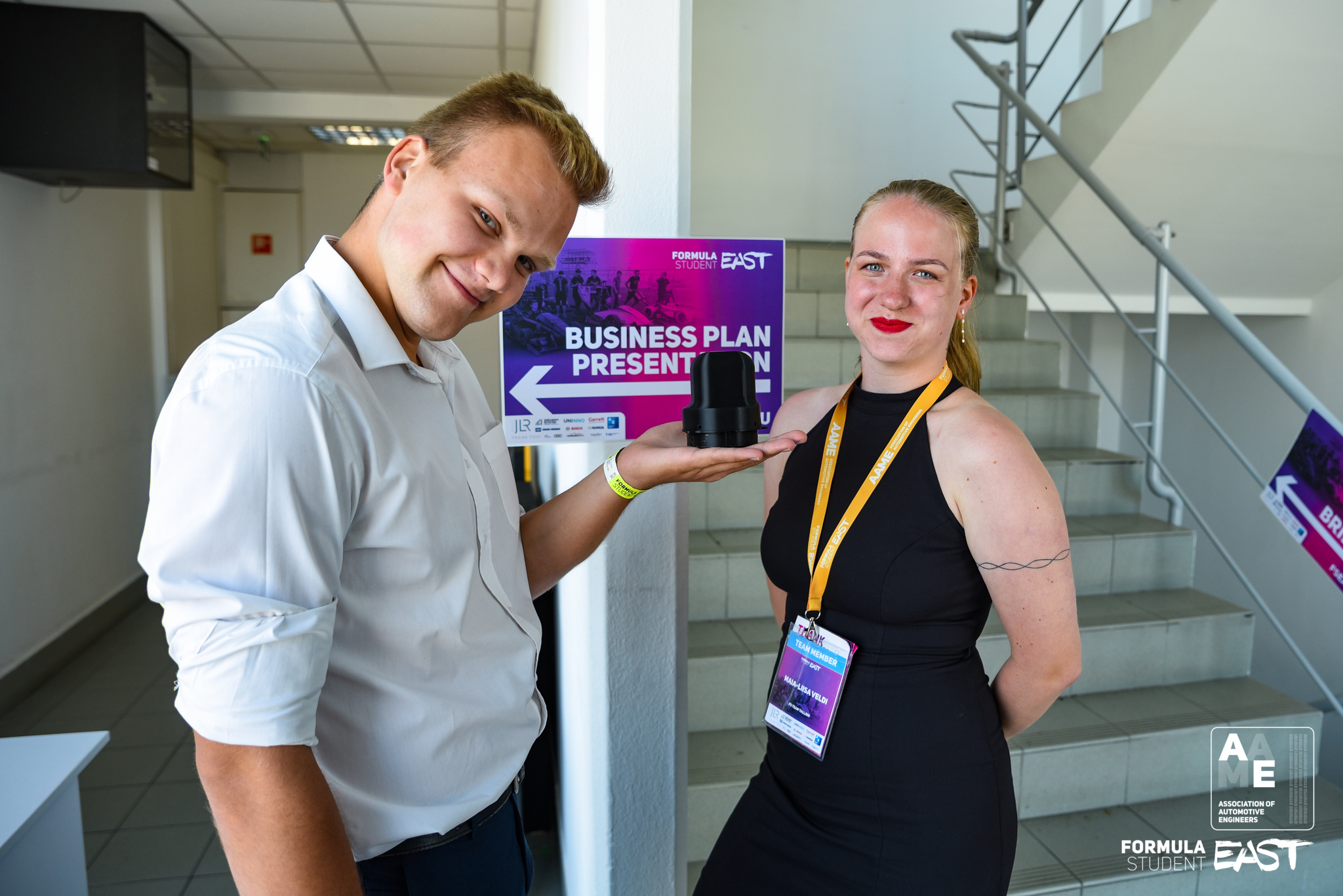
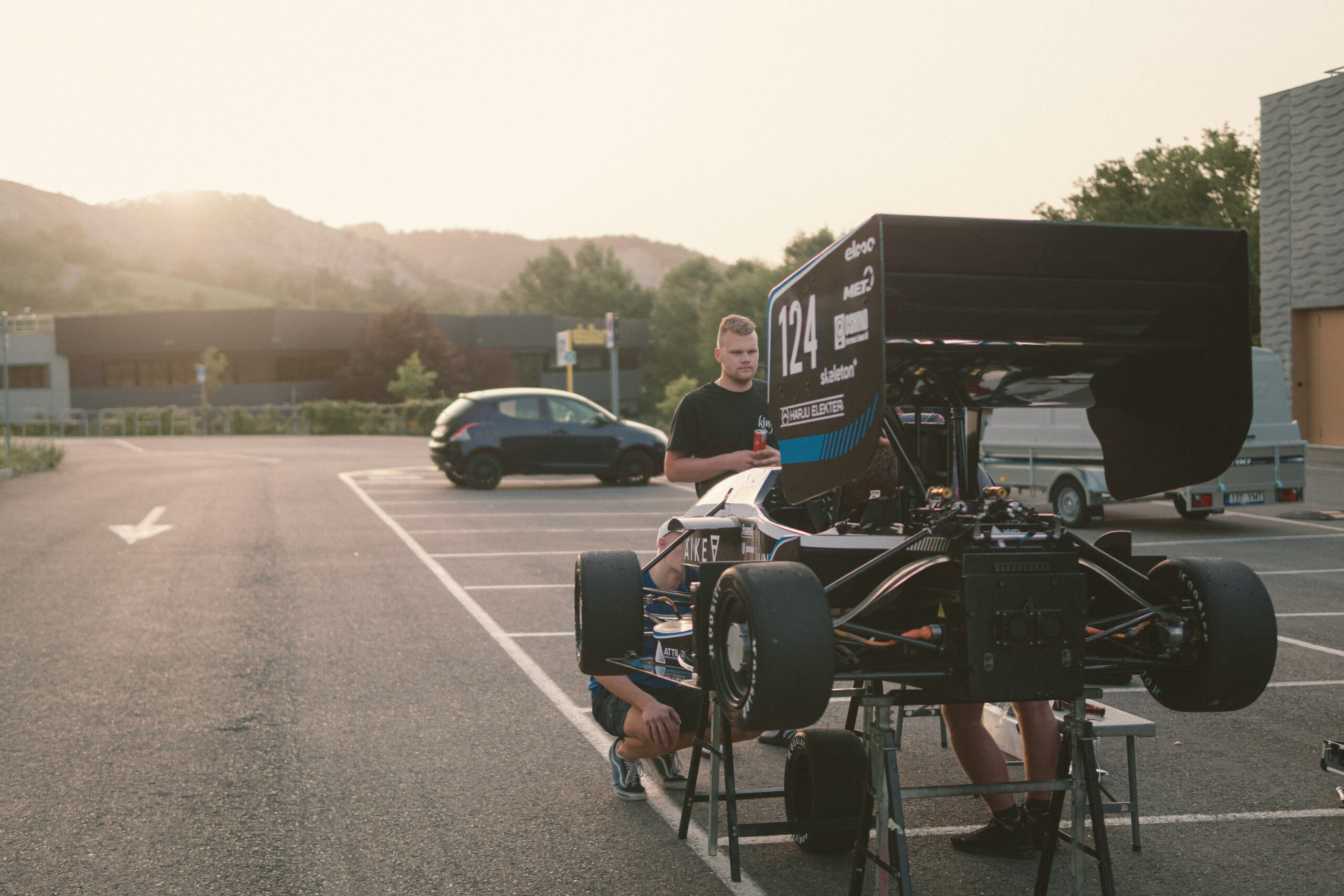
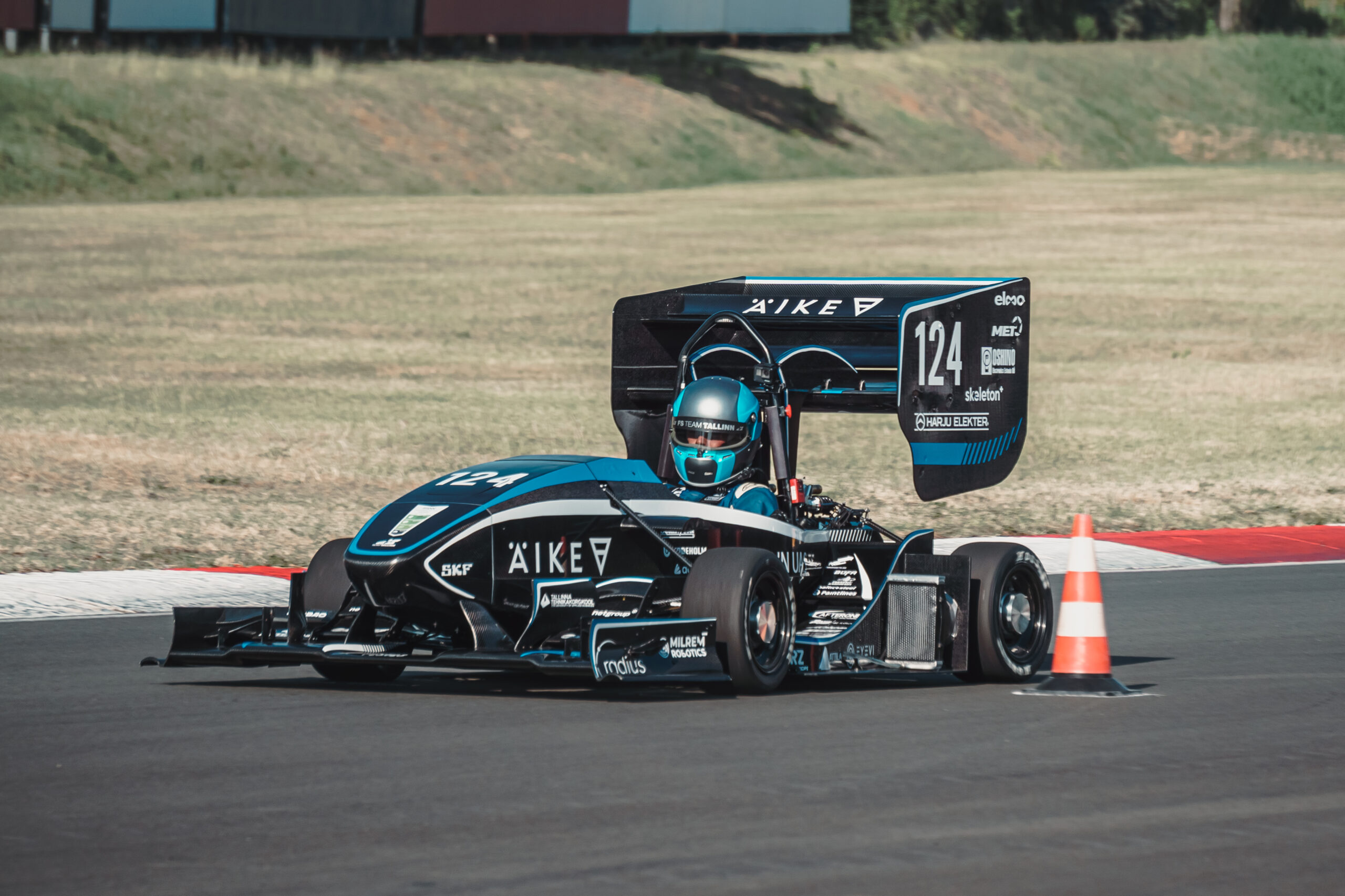
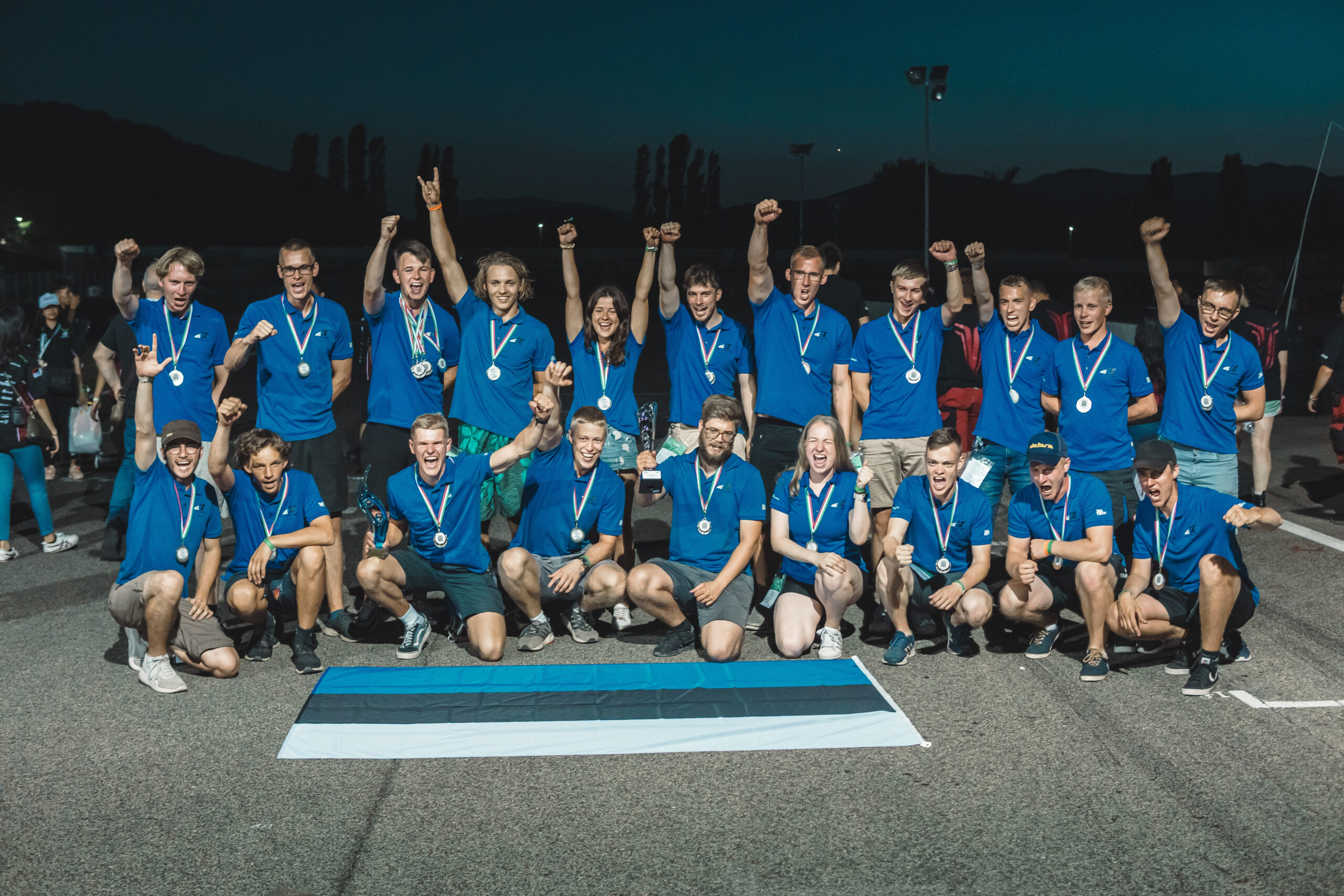
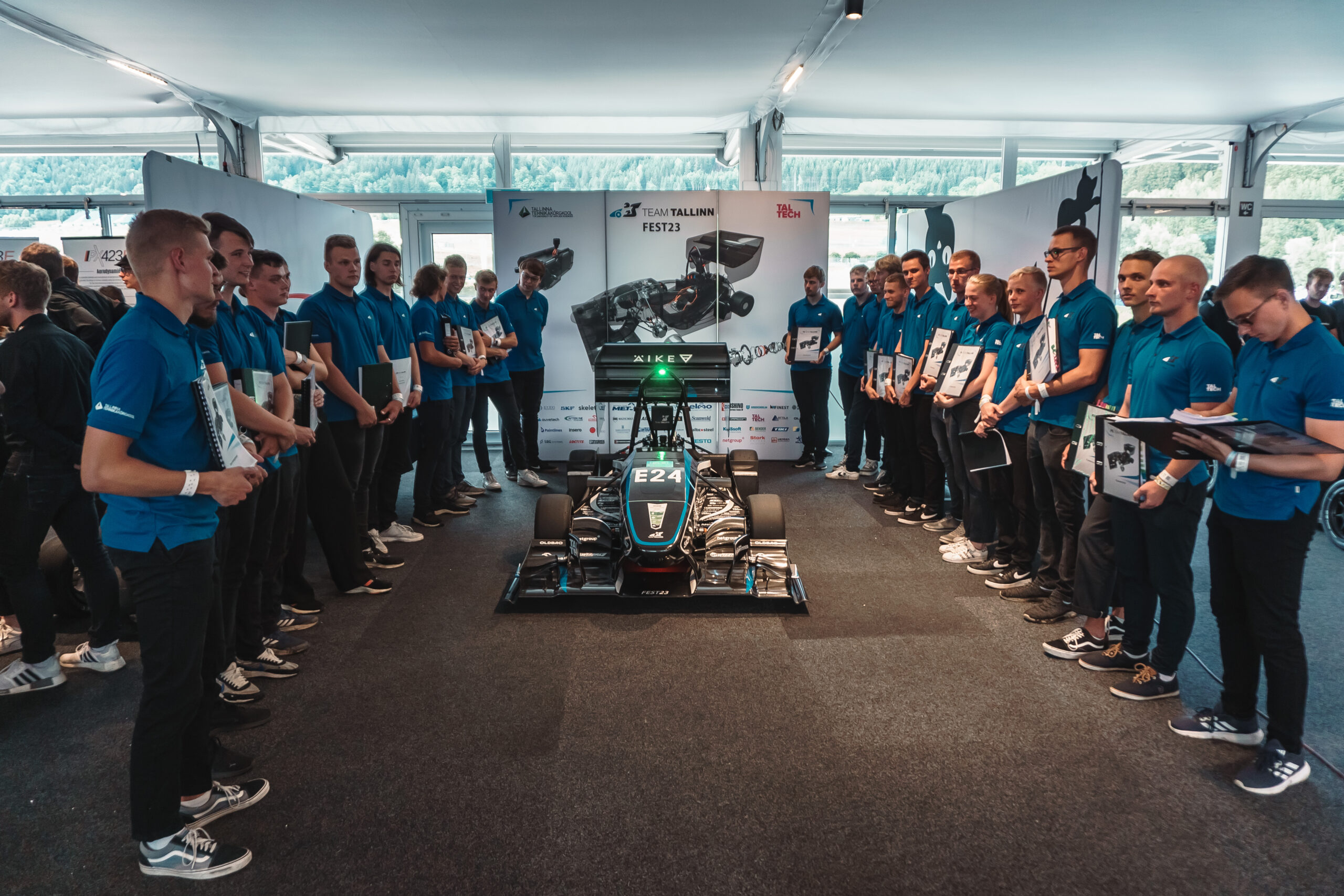
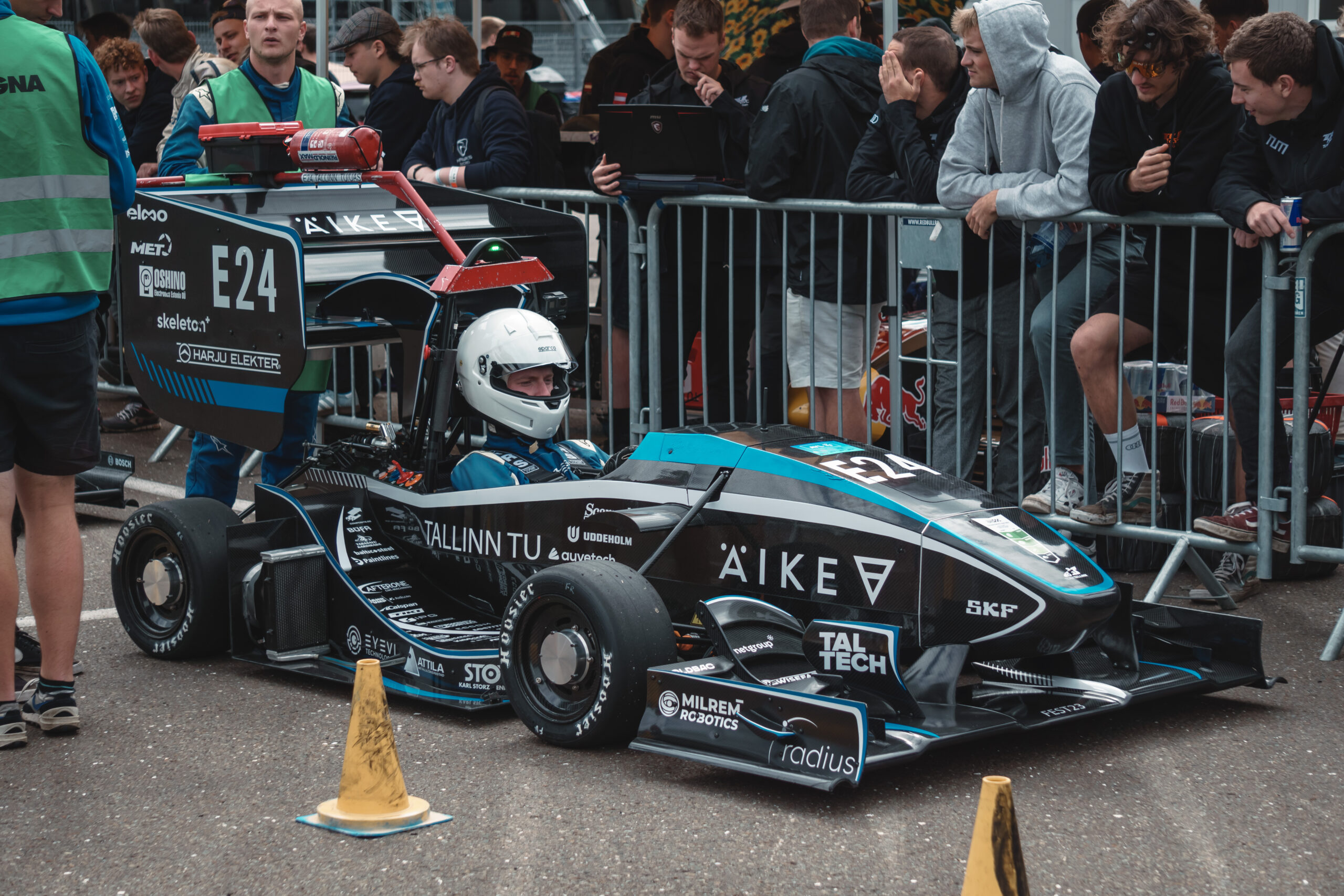
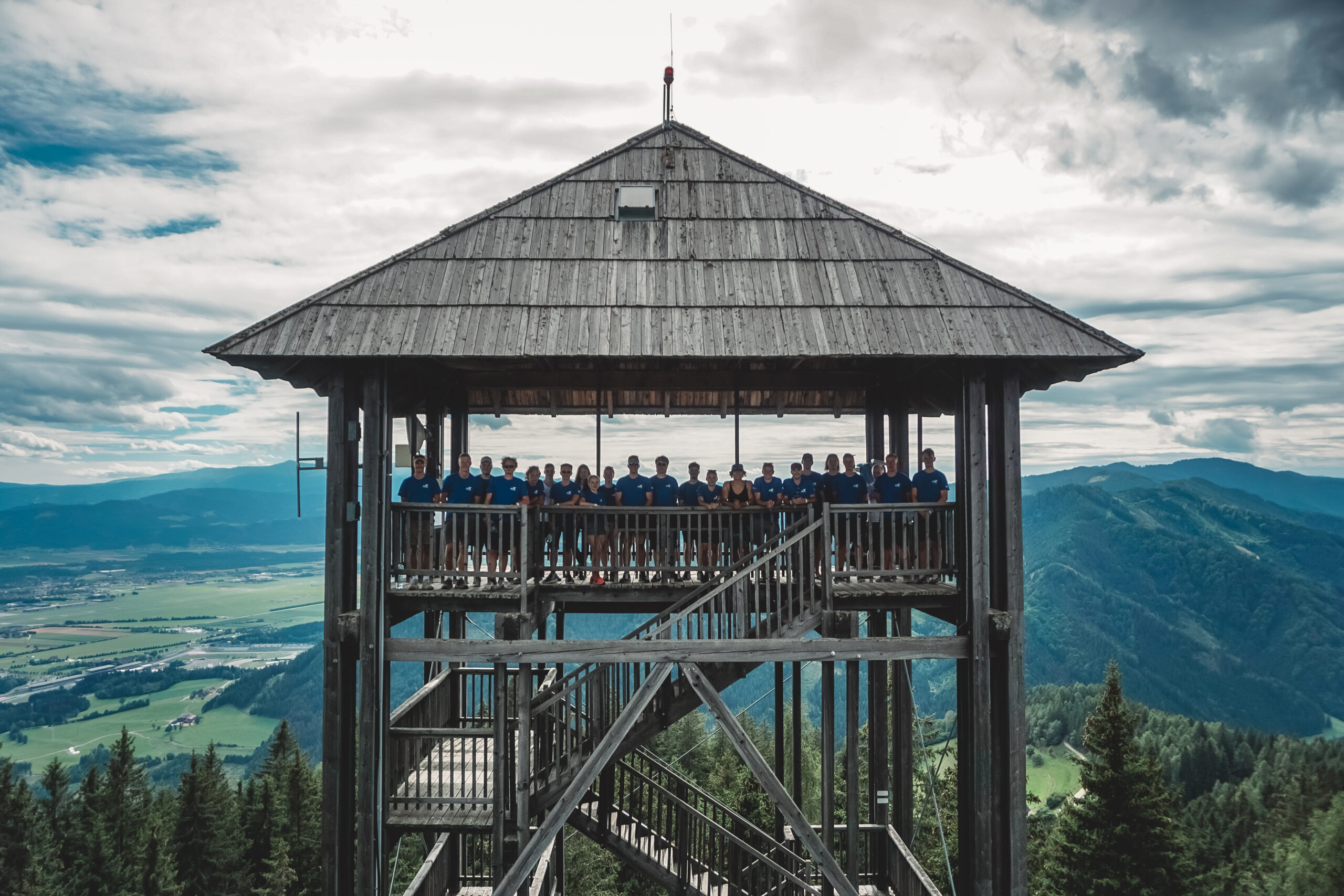
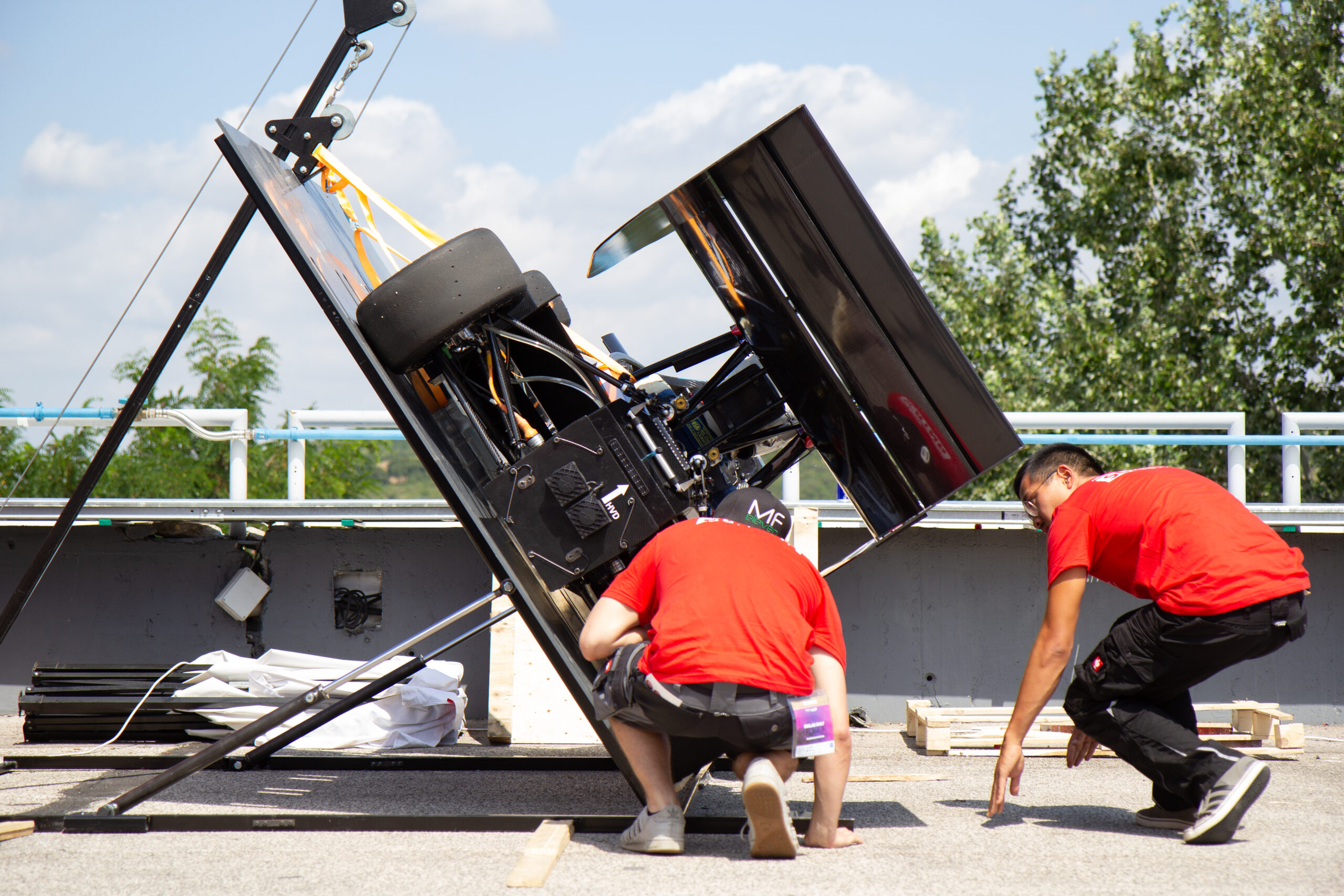
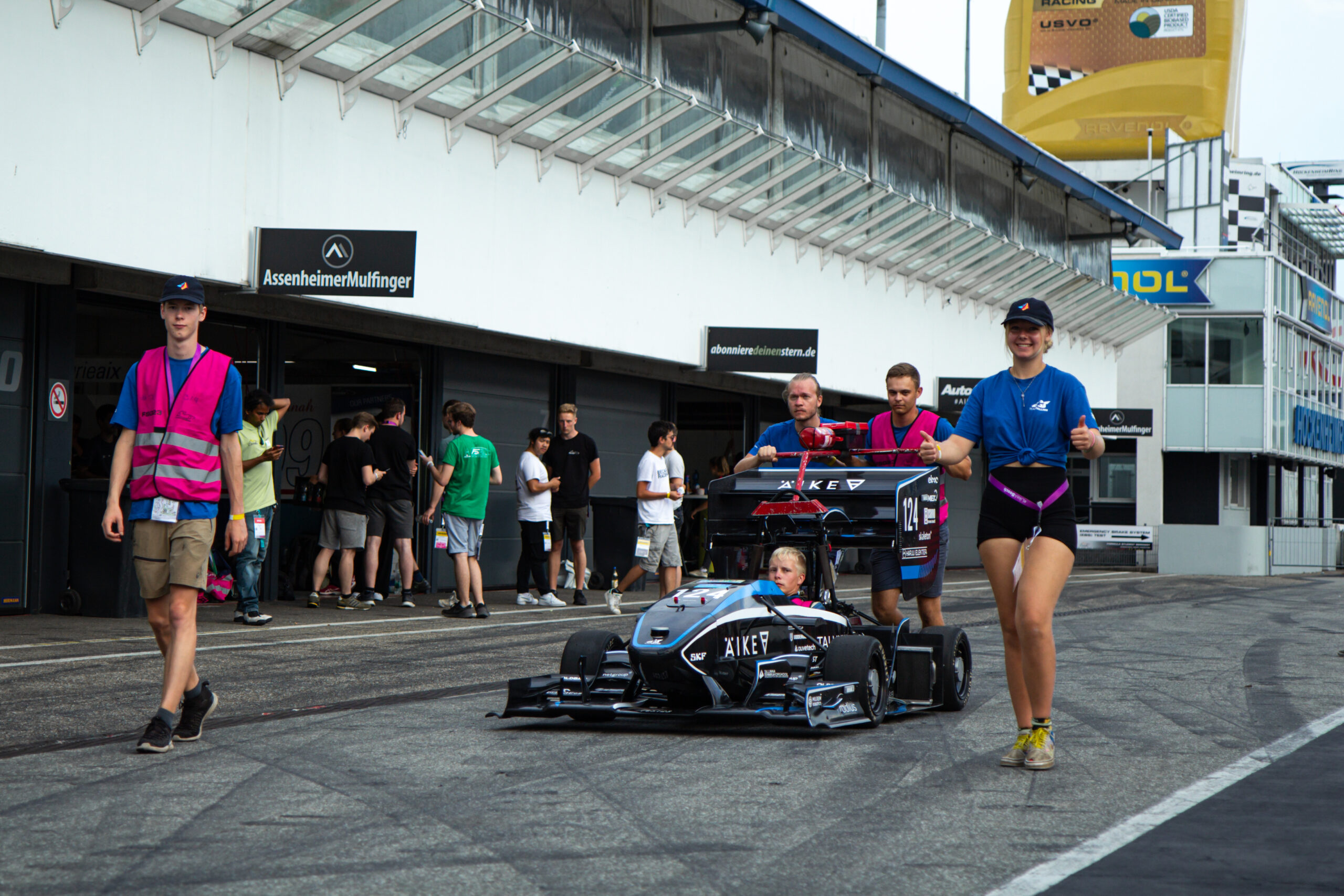
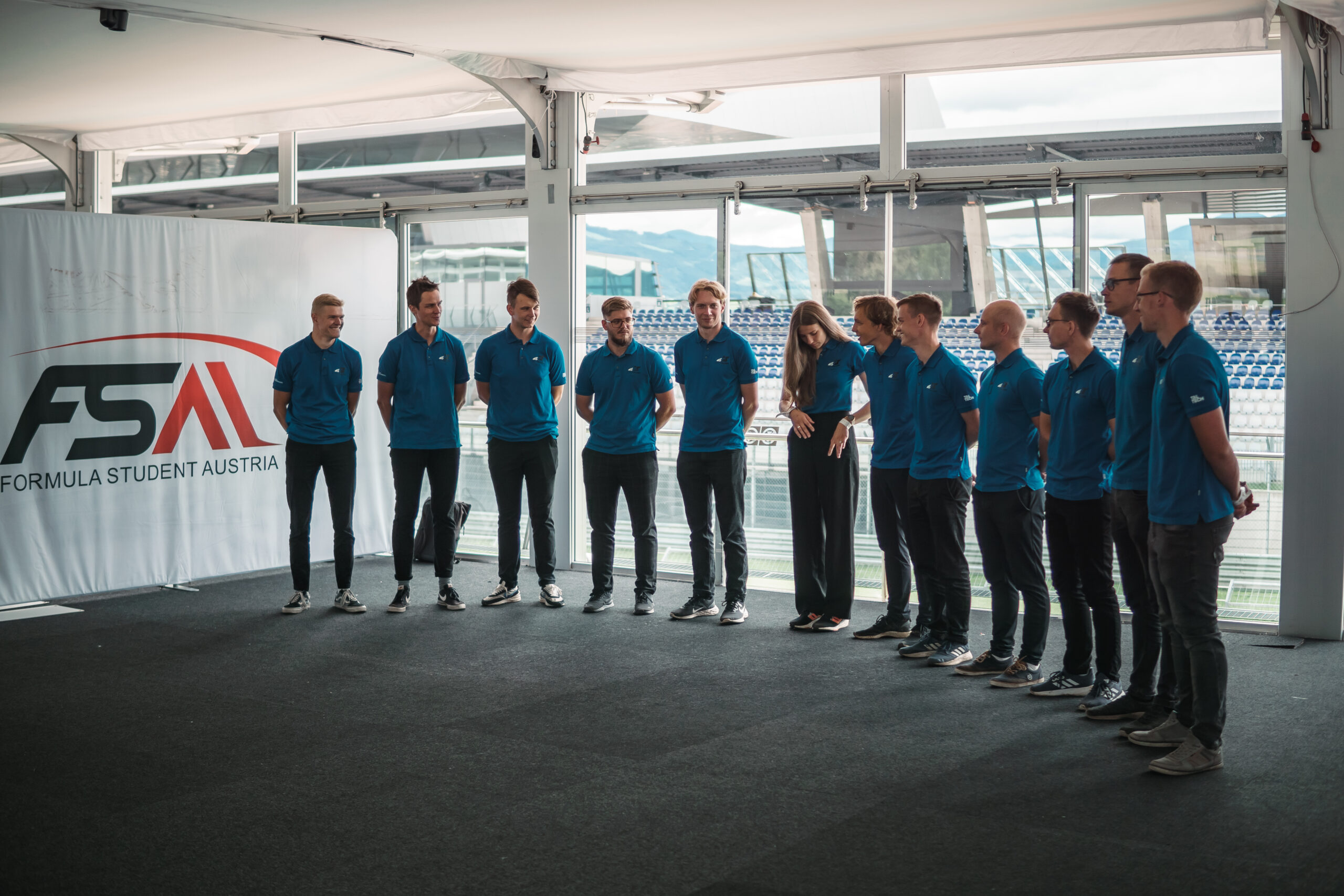
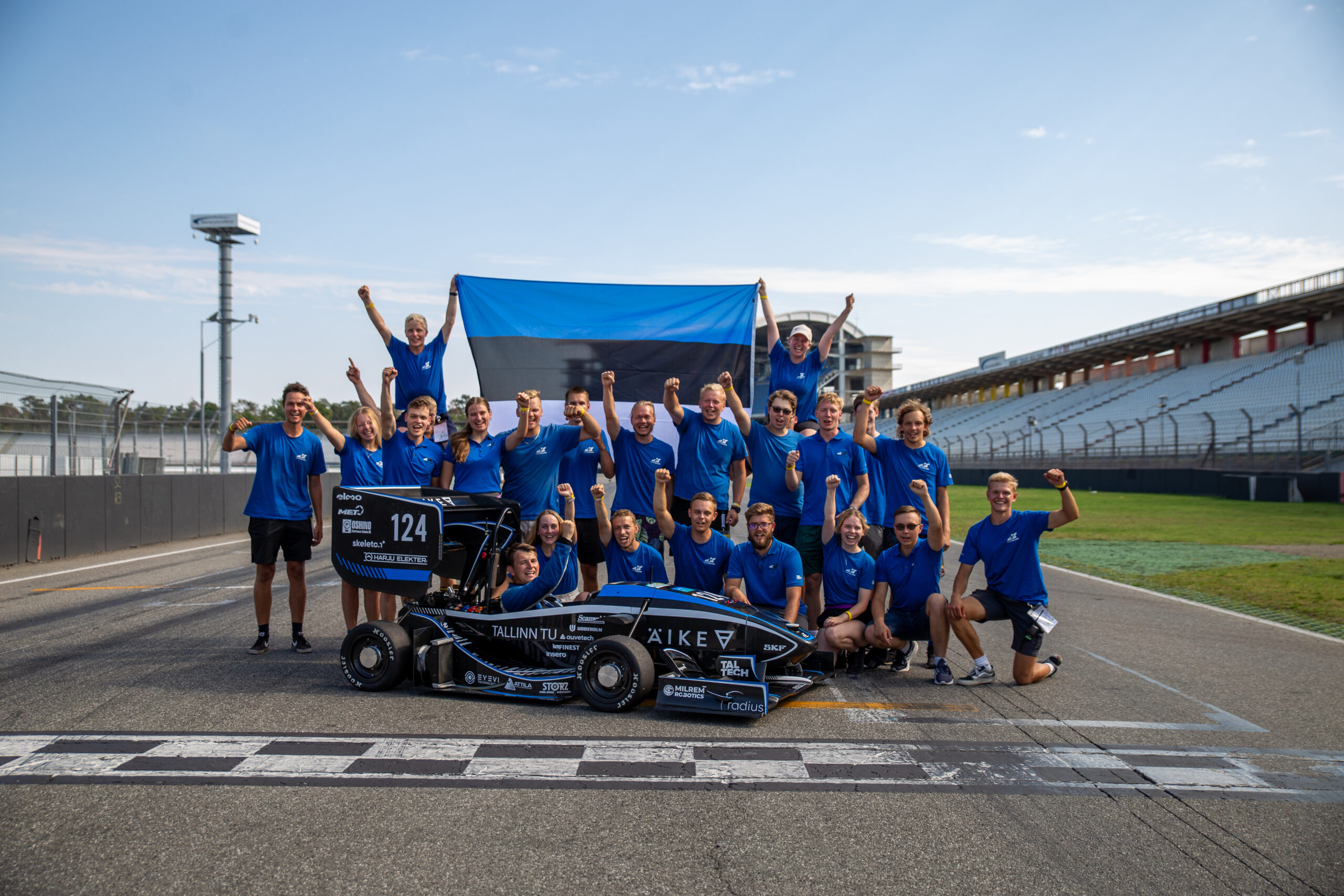
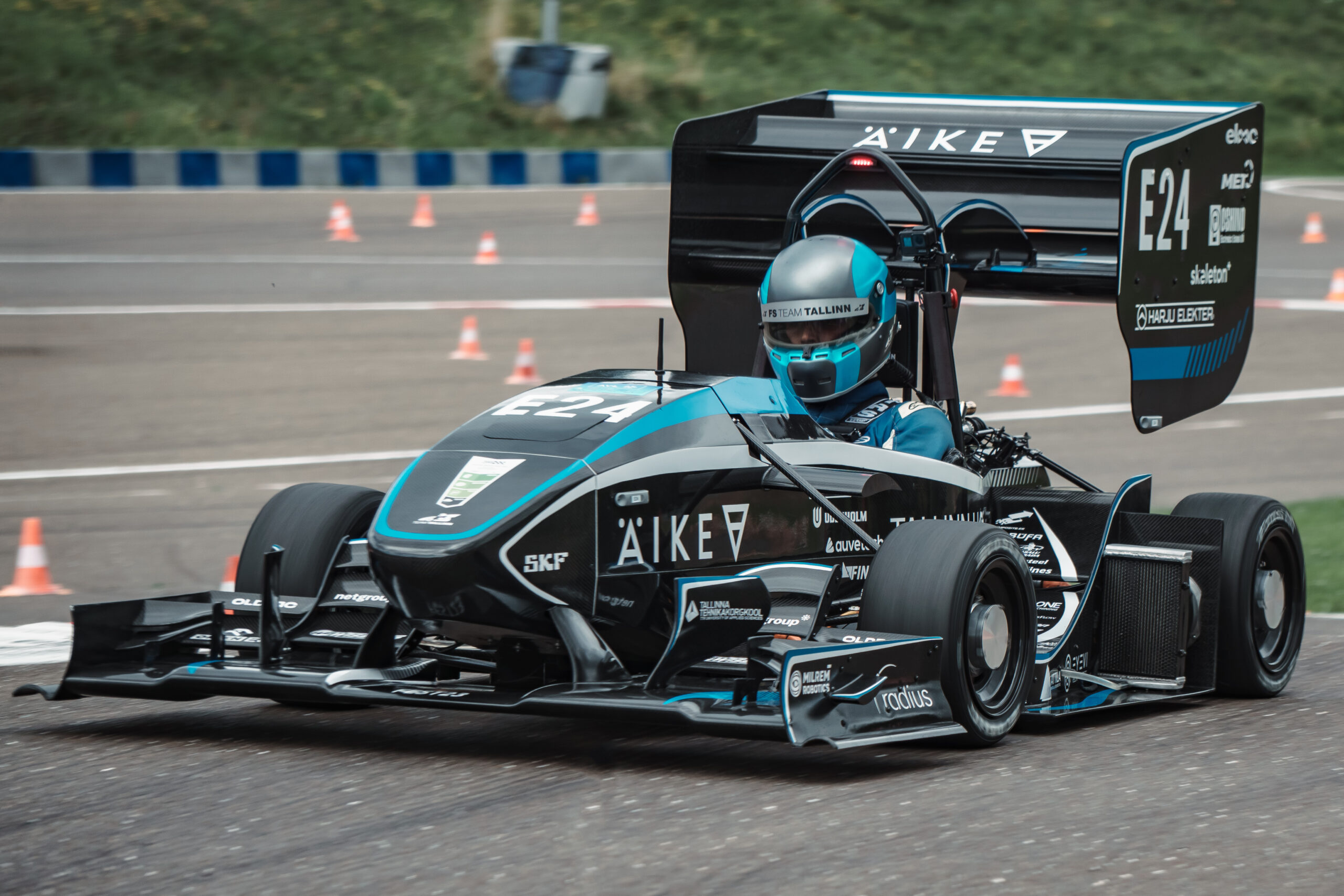
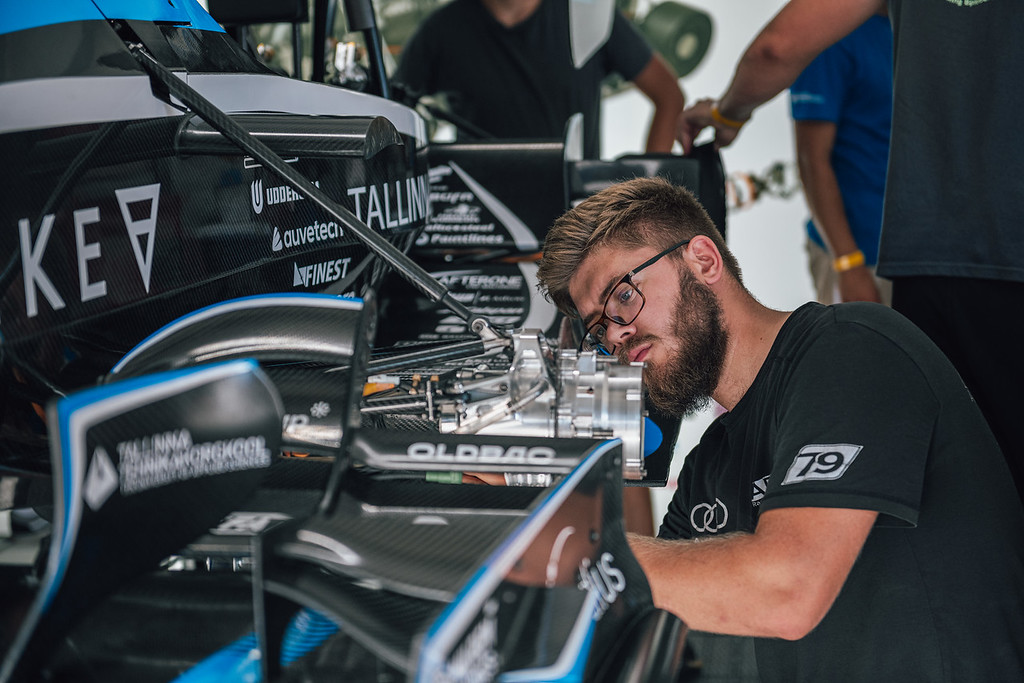
FS Austria
Cost: 3. place
Skidpad: 6. place
Acceleration: 6. place
Autocross: 10. place
Overall: 12. place
FS Germany
Qualifications: 3. place
Engineering Design: 4. place
Endurance: 6. place
Efficiency: 7. place
Acceleration: 8. place
Autocross: 10. place
Overall: 6. place
FS Italy
Acceleration: 1. place
Autocross: 2. place
Endurance: 2. place
Skidpad: 2. place
Overall: 2. place
FS Alpe Adria
Engineering Design: 1. place
Cost & Manufactoring: 1. place
Acceleration: 2. place
Business Plan Presentation: 2. place
Skidpad: 2. place
Autocross: 3. place
Overall: 11. place
FS East
FEST22
Engineering Design: 1. place
Acceleration: 4. place
Skidpad: 4. place
Autocross: 8. place
Overall: 11. place
Driverless
Engineering Design: 5. place
Cost & Manufactoring: 6. place
Overall: 15. place
Management
The Sub-Teams
- Administrative
- Composites
- Driverless
- Dynamics
- Electronics
- Powertrain
- Suspension
The general aim of the Admin sub-team is to raise awareness of the Formula Student team through variety of events, social media, and other means. Moreover, this sub-team takes care of finding partners, who would like to contribute to the project and support future engineers. Besides that, all the memories are captured and content for social media are taken care by the Admin sub-team. Last but not least, to create and maintain the website and to develop Business Plan Presentation are also two of many tasks that the Admin sub-team performs.
Saara Suurkivi
Chief of Admin
TalTech Food and Biotechnology BSc
FEST23
Risto Pärn
Videographics
TalTech Product Development and Robotics BSc
FEST23
Cer-Lyn Luhasaar
Website & Graphic Design
TalTech Business Information Technology BSc
FEST23
Karoliina Mustkivi
Sponsors & Marketing
TalTech Business BSc
FEST23
Akvile Svidrate
Events
TalTech Law BSc
FEST23
The work of the sub-team consists in the design and production of parts from composite materials. The biggest projects under the responsibility of the composite team are the structural solutions of the formula’s monocoque, accumulator container, firewall and the entire aerodynamics package. Self-developed calculation modules, manual calculations and FEM analysis are used in the design of parts. In addition, production drawings are made for each part. Depending on the geometry of the part and the required tolerances, the production technology is developed and the moulds required for production are designed.
Henri Nurmela
Ergonomics, steering wheel & head restraint
TalTech Electrical Power Engineering and Mechatronics BSc
FEST22/23
Karl Robin Tiislär
Chief of Composites
TalTech Product Development and Robotics BSc
FEST22/23
Sebastian Mikael Magagni
Monocoque CAD
TalTech IT Systems Development BSc
FEST21/22/23
Henri Nurmela
Ergonomics, steering wheel & head restraint
TalTech Electrical Power Engineering and Mechatronics BSc
FEST22/23
Mikk Saarse
SES
TalTech Integrated Engineering BSc
FEST22/23
Erko Elbrecht
Aero Structures
TalTech Structural Engineering and Construction Management BSc
FEST23
Tanel Palmsaar
Firewall
TalTech Product Development and Robotics BSc
FEST22/23
Robin Hendrik Vint
LiDAR Mounting
TTK Automotive Engineering BSc
FEST23
Sven Rosenberg
Aero Structures
TalTech Electrical Power Engineering and Mechatronics BSc
FEST23/22/21/20
The driverless team develops the software needed to drive the formula autonomously without human assistance. The tasks of the team can be put into three major categories. First, seeing and perceiving the world, which includes the collection and processing of data from various sensors. Second, it is necessary to understand the position and orientation of the vehicle in the world, and it is also necessary to create a virtual environment for it. The data obtained in the previous category will be used for this task. Thirdly, it is necessary to plan the path and control the formula car. To do that, the position of the car and understanding of the virtual environment will be used.
Karl Mihkel Seenmaa
Chief of Driverless
TalTech Informatics BSc
FEST21/22/23
Anton Osvald Kuusk
Computer
TalTech Informatics BSc
FEST20/21/22/23
Ott Kärner
SLAM
TalTech Product Development and Robotics BSc
FEST21/22/23
Helar Pullisaar
Velocity planning
TalTech Product Development and Robotics BSc
FEST22/23
Joel Joshua
LiDar
TalTech Integrated Engineering BSc
FEST22/23
Lisanne Siniväli
Path planning
UT Informatics MSc
FEST20/21/22/23
Tanel Tallo
SLAM
TalTech Informatics BSc
FEST23
Marten Vooro
Control
TalTech Informatics BSc
FEST23
Anna Sihvart
Control
TalTech Product Development and Robotics BSc
FEST23
The members deal with the evaluation and influence of the physical phenomena affecting the vehicle, with the aim of achieving its maximum potential. The team’s responsibilities include concept development, lap time simulation, suspension kinematics, aerodynamics, control system and general vehicle dynamics. In addition to their own responsibilities, members have an important role in providing design input to other engineers. Unlike other subteams, the work of dynamics is theoretical, but affects the vehicle the most.
Mattias Laos
Chief of Dynamics
TTK Mechanical Engineering BSc
FEST20/21/22/23
Maano Maasikmets
Aerodynamics & CFD
TalTech Product Development and Production MSc
FEST20/21/22/23
Raul Kaarlõp
Aerodynamics & CFD
TalTech Structural Engineering and Construction Management BSc
FEST22/23
Markus Männi
Aerodynamics & CFD
TalTech Product Development and Robotics BSc
FEST22/23
Morgan Puust
Control System
TalTech Informatics MSc
FEST20/21/22/23
Robert-Juss Soe
Kinematics & Tire Data & Driver
TTK Mechanical Engineering BSc
FEST22/23
Oskar Järg
Control System & ECU
TalTech Product Development and Robotics BSc
FEST21/22/23
Maik Salla
Aerodynamics
TalTech Road Engineering and Geodesy BSc
FEST23
Ben Eilaste
Aerodynamics
TalTech Product Development and Robotics BSc
FEST23
Raul Mihkel Anton
Aerodynamics
TalTech Product Development and Robotics BSc
FEST23
The sub-team is responsible for the vehicle’s low-voltage system. The team members are mainly involved in the design and production of wiring and printed circuit boards and programming of certain boards. The vast majority of circuit boards in the car are self-developed. The printed circuit boards have very different tasks: several safety systems, powering the low-voltage system, data acquisition, displaying information to the driver, and so on. The wiring connects all the electronic components together enabling communication through the CAN network.
Danel Tiitma
Chief of Electronics
TalTech Hardware Development and Programming BSc
FEST22/23
Artur Lindegron
PWD
TTK Robotics Engineering BSc
FEST20/21/22/23
Ergo Adams
Ground Speed Sensor
TalTech Applied Physics BSc
FEST23
Karl J. Terasmaa
PCB Development
TalTech Product Development and Robotics BSc
FEST23
Mart Dudin
LV Wiring
TalTech Integrated Engineering BSc
FEST23
Maia-Liisa Veldi
LV Wiring
TalTech Electrical Power Engineering and Mechatronics BSc
FEST23
Nazar Atamanenko
LV Wiring
TTK Robotics Engineering BSc
FEST23
The task of the powertrain team is to make the formula drive using the electrical energy stored in the accumulator. For this, the engineers of the sub-team design a accumulator with the required capacity and voltage, the most efficient voltage converter and motors, a planetary gearbox with a suitable transmission ratio and the cooling system. Since most of the mentioned components contain high voltage, great emphasis is placed on safety and reliability. For this purpose, both manual calculations and analysis programs are used for each system, and the results are validated in the form of real tests.
Raigo Seppago
Chief of Powertrain
TalTech Electrical Power Engineering and Mechatronics BSc
FEST21/22/23
Martin Meras
Motors
TalTech Energy Conversion and Control Systems MSc
FEST21/22/23
Hans Anniste
Self-developed Inverter
TalTech Electronics and Communication Technologies MSc
FEST19/20/22
Maiko Mägi
Accumulator
TTK Automotive Engineering BSc
FEST21/22/23
Karl Rasmus Uibo
Controller
TalTech Product Development and Robotics BSc
FEST23
Robin Saarniit
Cooling System
TTK Automotive Engineering BSc
FEST22/23
The sub-team learns to design and manufacture mechanical systems. The team’s task is to make the braking and steering system, the suspension and everything related to it – they design all the parts that connect the monocoque to the asphalt. All parts are subjected to strength calculations or FEM analysis, correct production drawings are made before production and tolerance chains are determined.
Robin Saarniit
Chief of Suspension & Driver
TTK Automotive Engineering BSc
FEST22/23
Jaanika Kiolein
Steering System, Corner Assembly & Braking system
TalTech Product Development and Robotics BSc
FEST21/22/23
Madis Laaser
Brake System
TalTech Product Development and Robotics BSc
FEST22/23
Risto Pärn
Bellcrank
TalTech Product Development and Robotics BSc
FEST23
Kener Sumla
Mounting brackets
TalTech Product Development and Robotics BSc
FEST23
Heldur Hanni
Anti-roll Bars
TalTech Integrated Engineering BSc
FEST23